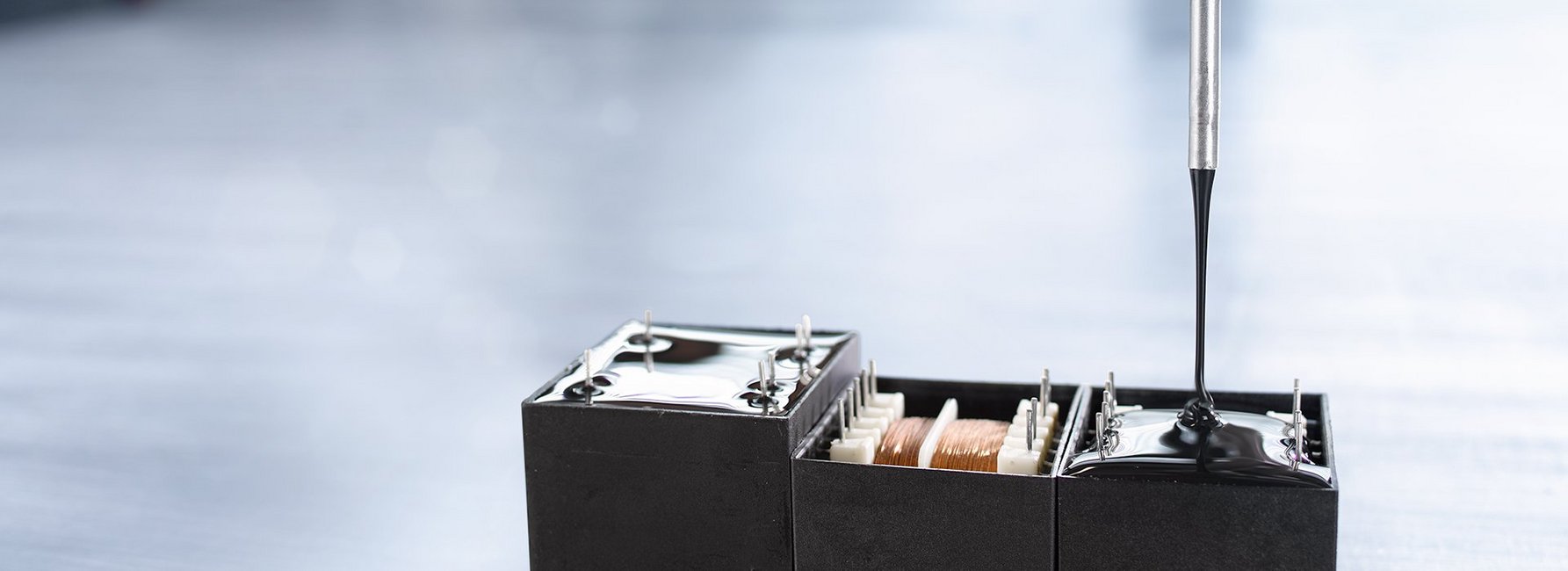
Effective. Enduring.
Processing of Reactive Plastic Systems
Developing process technology for sealing, casting, and bonding single-, dual-, and multi-component reactive plastic systems is the core competence of RAMPF Production Systems.
We specialize in
- Project planning for customer-specific production systems with integrated dispensing processes
- Manufacturing turnkey production systems with a standardized user interface and integrated measuring and data management
- Global service support through our own branches and partners
Our customer-specific solutions include integrating both surface activation processes as well as testing and measuring technology to safeguard production processes.
Together we will find the best solution for your application. Why? Because of the comprehensive application experience we have gathered from the implementation of over 3,000 projects across the globe.
Dispensing Systems for Thermal Conductive Materials
Casting systems based on epoxy, silicone, and polyurethane all serve different purposes in the electronics industry. Resin encapsulates protect sensitive electronic components from contact, dust, and moisture, and manufacturers put in different fillers and additives to custom-fit the materials to meet customer requirements. The additives, and especially their distribution within the components that are being dispensed, place particularly high demands on the pumping system. This is why selecting the proper dispensing pump has such a decisive influence on process reliability.