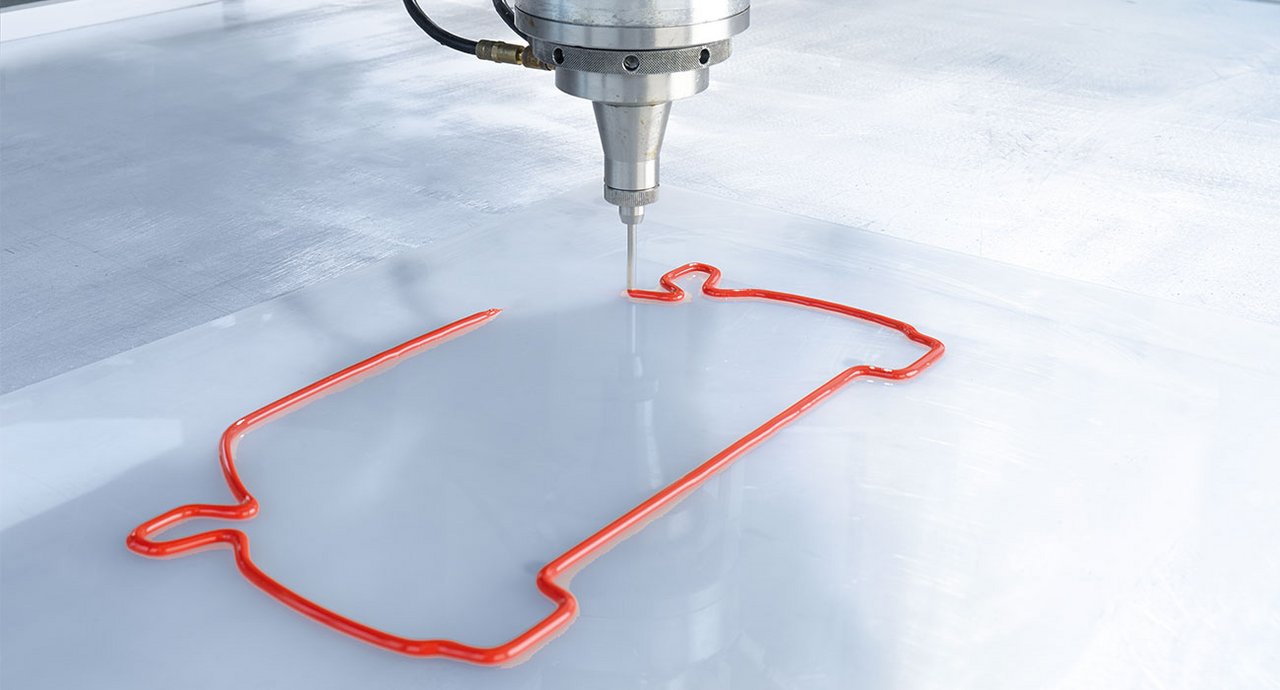
MECSPE 2019 – High-performance Reactive Resins & End-to-End Production Systems
The international RAMPF Group is attending Italy’s largest specialist plastics trade fair MECSPE in Parma for no less than the ninth time. From March 28 - 30, high-performance reactive resins for sealing, casting, and bonding will take center stage alongside end-to-end production systems with integrated dispensing technology – Booth G25, Hall 6.
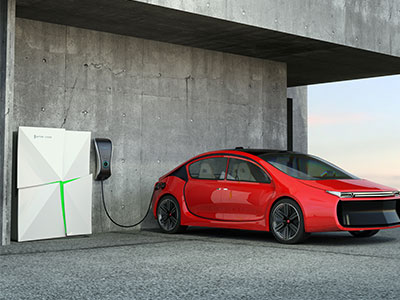
RAMPF Polymer Solutions is displaying its new silicone foam that cures within minutes of application at room temperature. This cuts out the oven-curing typically associated with silicone foam, making installation faster and saving an entire production step. Further advantages include its low hardness (Shore 00), low compressive strength for low installation forces, and high chemical and temperature resistance. Applications include battery covers, engine compartment gaskets, and control cabinets in explosive environments and outdoors.
> Foam gaskets for the automotive industry
RAKU® PUR and RAKU® SIL foam gaskets from RAMPF Polymer Solutions are used throughout automotive construction. Their outstanding mechanical properties, excellent adhesion to almost all plastic materials, and short tack-free time make these polyurethane and silicone systems the got-to-product for a wide range of applications. Low-emission options are available for automotive interiors. Applications include door modules, brake lights, headlights, taillights, electrical enclosures, ignition coil covers, fuse boxes, ventilation grills, speakers, panels etc.
> RAKU® PUR Speed – faster than ever
The new generation of RAKU® PUR Speed quick-curing polyurethane foam gaskets has been developed specifically for ultrafast process chains in automotive manufacturing. These gaskets are ready for use less than three minutes after application, freeing up production areas and making them ideal for lean manufacturing. The foam gaskets are designed for use in both 2D and 3D applications and meet the standards required by leading OEMs.
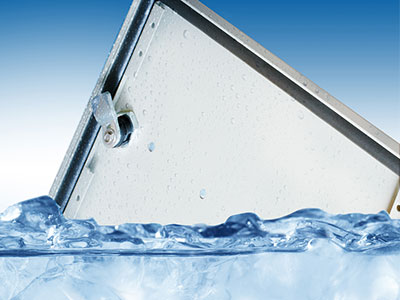
Two-component foam gaskets, casting systems, adhesives, and reactive hotmelt adhesives from RAMPF Polymer Solutions achieve first-class results in the filter industry. The good flow characteristics of the compact two-component PU casting systems and short curing times significantly speed up the casting processes used in the manufacture of air filters. The good adhesive characteristics on plastic (particularly ABS and PS) help improve the stability of the filter elements. Depending on the requirements of the application, these polyurethane systems are available as antibacterial and silicone/silane-compound-free formulations.
> Sealing, casting, and adhesive systems for manufacturing filters
Two-component foam gaskets, casting systems, adhesives, and reactive hotmelt adhesives from RAMPF Polymer Solutions achieve first-class results in the filter industry. The good flow characteristics of the compact two-component PU casting systems and short curing times significantly speed up the casting processes used in the manufacture of air filters. The good adhesive characteristics on plastic (particularly ABS and PS) help improve the stability of the filter elements. Depending on the requirements of the application, these polyurethane systems are available as antibacterial and silicone/silane-compound-free formulations.
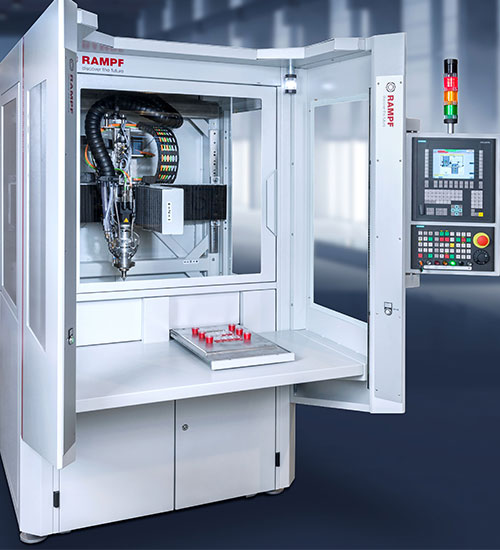
Compact, flexible, high-performance – the DC-CNC800 dispensing system for dynamic sealing, bonding, and casting from RAMPF Production Systems. The system features a built-in material preparation unit and can be fitted with high-precision piston or gear pumps. A CNC Siemens Sinumerik control system and Beckhoff control technology are available for modular control. A further advantage is the integrated process monitoring that oversees pressures, fill levels, and speeds.
The DC-CNC800 can be fitted with a high-pressure rinse agent recycling system, high-pressure water rinsing, various application-specific automation systems, and the MS-C mixing system for dispensing rates of 0.1 g/sec and above. Its large tanks facilitate the filling of small containers in a single step. Additional features include standardized operating concepts for shuttle table, rotary index plate, and conveyor feed, together with vacuum barrel presses. Accessibility has been optimized for maintenance work on the piston or gear pumps and controls.
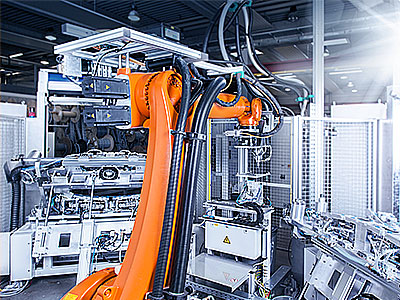
Process expertise combined with the optimal automation solution generates maximum customer benefit. In addition to its core competence of mixing and dispensing technology, RAMPF Production Systems develops customized automation systems, such as for handling and robotics, component transportation, control technology, and capturing all process parameters with MES connection.
The company’s process automation portfolio also includes tool and equipment construction, material pre-treatment (activation), heat treatment, image processing, sensors, and contactless measuring technology.