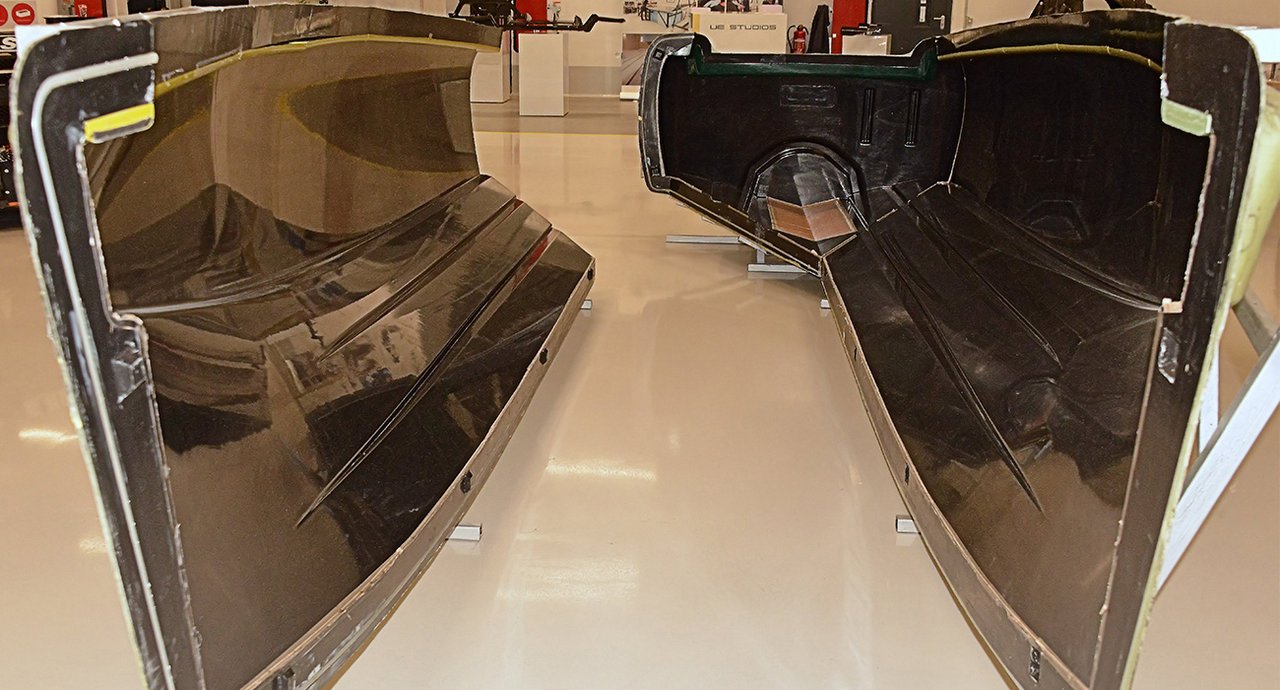
Pioneering lightweight construction in theory and practice
Grafenberg, November 16, 2017. High-caliber speakers and a spectacular in-house exhibition made sure the latest trends in lightweight construction using fiber composites were put well and truly center stage at the RAMPF Composites Symposium. Some 120 participants and 21 exhibitors took up the invitation extended by RAMPF Tooling Solutions and attended the event at the brand-new production facility in Grafenberg.
Reducing weight while increasing mechanical strength – it may be very simplified, but it is a pretty accurate way of explaining the burgeoning popularity of fiber composites. Companies in a whole range of industries, but first and foremost in the automotive, aerospace, boat and shipbuilding, medical technology, mechanical engineering, and sports and leisure sectors are working intensely on testing which of their products can be manufactured using composites to boost performance.
Thanks to their products and processes, customers and business partners of RAMPF Tooling Solutions and the specialists from the Grafenberg-based company itself are among the market leaders in the aforementioned industries. As part of the RAMPF Composites Symposium, these experts displayed their know-how in numerous presentations and an encompassing in-house exhibition.
The presentations examined topics including the potential of cyanate ester for the resin infusion process, the processing and finishing of a CFRP fender, and the use of RAKU® TOOL Close Contour Castings in the manufacture of aircraft components.
Liquid, paste, and board materials for high-tech products
After the presentations, participants had the opportunity to check out some truly impressive products and solutions for lightweight construction, courtesy of 21 exhibitors and the six RAMPF Group companies. The venue for the exhibition was the brand new production facility, where RAMPF Tooling Solutions will start producing polyurethane and epoxy styling, modeling, and working boards early next year.
The exhibits included a production mold for a boat hull that measured several meters in length and had been made using resin infusion, a prepreg lay-up tool for the production of a car roof, a glass-fiber lay-up tool for manufacturing a cockpit cover, and a gyro-stabilized camera mount that had been produced using the VARI (Vacuum Assisted Resin Infusion) technique.
“We are always very impressed by the products and solutions of our customers and business partners,” emphasizes Jochen Reiff, Managing Director of RAMPF Tooling Solutions. “We are proud that our liquid, paste, close contour, and board materials are used for the production of such high-tech, high-quality products.”