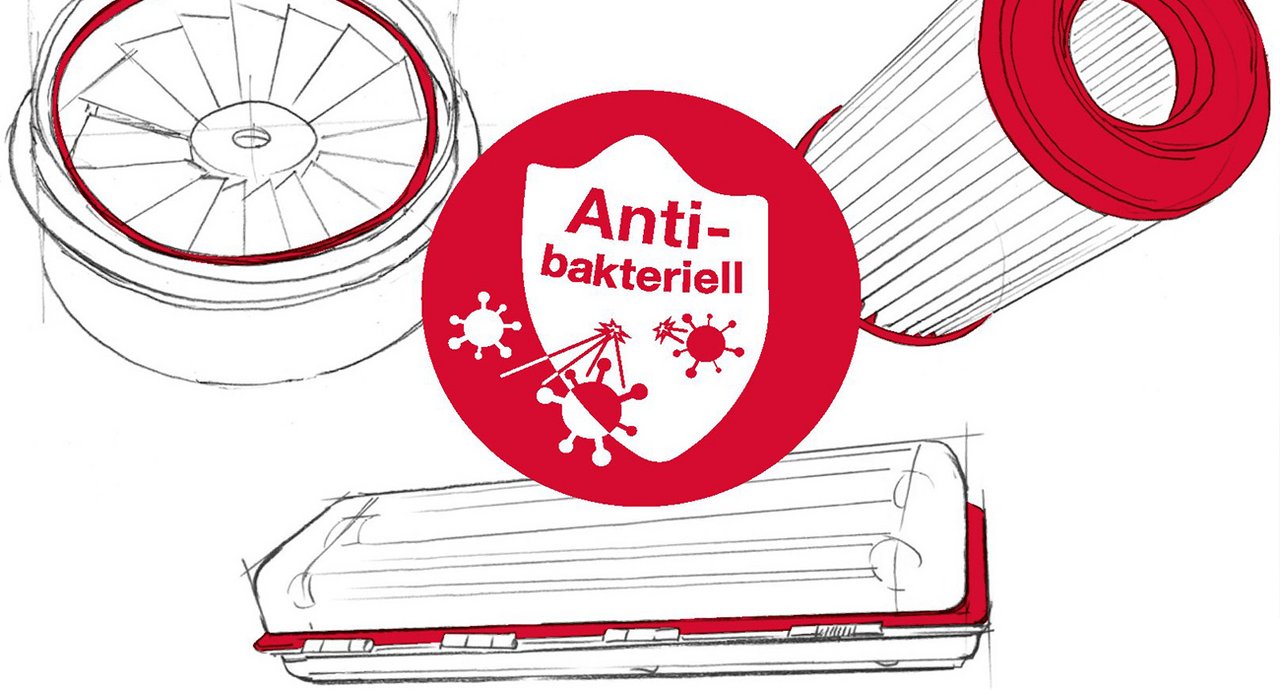
Efficient industrial production with materials and machinery from RAMPF
The RAMPF Group is showcasing innovative foam gaskets, construction casting resins, filter casting and bonding systems, as well as high-performance dis-pensing robots and desktop dispensing cells along with its Italian partner Cabelpiù at MECSPE 2016 in Parma, Italy from March 17 to 19 – Hall 6, Stand F26.
The joint RAMPF and Cabelpiù stand at MECSPE 2016 is the one-stop-shop for materials and machinery for sealing, foaming, casting, design, and bonding in numerous industrial applications.
RAMPF Polymer Solutions, a leading developer and manufacturer of reactive plastic systems based on polyurethane, epoxy, and silicone, will be showcasing the following product highlights:
RAKU-PUR® 32-3276 antibacterial foam gasket
The microbially inert RAKU-PUR® 32-3276 foam gasket is used to reliably seal air conditioning equipment, ventilation systems, and cleanroom lighting, e.g. in hospitals, offices, production halls, and concert halls.
The sealing system is bacteriostatic and fungistatic, so fungus and bacteria have no chance of establishing themselves on the thixotropic material. Combined with its high tear resistance, low water absorption, extremely compact and hydrophobic integral skin, and outstanding adhesion on metal surfaces, RAKU-PUR® 32-3276 is the number one choice when it comes to meeting the strictest hygiene requirements.
RAKU-PUR® 32-3264 and RAKU-PUR® 32-3278 low-emission foam gaskets
The RAKU-PUR® 2-component PUR foam gaskets are impressive in terms of their low emissions values, high mechanical strength, low water absorption, excellent bonding on metal, and high temperature resistance. The PUR systems, which are used for sealing as rattle protection (NHV noise, vibration, harshness), ensure the reliable, efficient, and low-emissions sealing of complex, three-dimensional com-ponent contours.
RAKU-PUR® 32-3264 and RAKU-PUR® 32-3278 have been tested to VDA 270, 275, and 278 and meet all physical-mechanical and emissions requirements, including the BMW Group’s TL 8350151 and Daimler AG’s DBL 5452.13. Their high viscosity ensures that the foams do not run, even on vertical surfaces, and form even beadings. The outstanding tear resistance of the RAKU-PUR® gaskets are more than able to resist the shear forces that can occur during installation.
RAKU-PUR® SPEED – tack-free in minutes
Apply, allow to foam, and the gasket is done. Once the foam has been applied, the component is suitable for immediate further processing – cost-intensive storage in curing ovens or storage systems is therefore a thing of the past. For industrial applications within complex production lines, e.g. in the automotive industry, where it has to be possible to handle the component immediately after the gasket has been applied, RAKU-PUR® SPEED technology provides an unbeatable advantage.
Other features of RAKU-PUR® SPEED include low water absorption and high mechanical strength for adhesion to various materials, from polypropylene to painted steel, in assembly operations. The material offers long-term temperature resistance in a range from -30°C to +90°C and can be exposed to tempera-tures ranging from -40°C to +140°C for short periods.
RAKU-PUR® construction resins for the strictest requirements
The high-performance casting resin systems are used for manufacturing components with high mechanical loads, including housings, covers, and impact-resistant technical parts.
RAKU-PUR® and RAKU-POX® casting systems for filter manufacturing
Thanks to their short process times, RAMPF casting systems enable perfect production processes for filters. Additional benefits include high temperature and chemical resistance. RAKU-PUR® and RAKU-POX® casting systems have been used successfully for years in the manufacture of oil and hydraulic filters, air filters (HEPA, ULPA), and waste water filters, among other things.
Bonding systems for mounting applications, sandwich elements, and surface lamination
RAMPF’s mounting adhesive portfolio includes PUR, epoxy, hybrid, silicone, and hot-melt adhesives that ensure reliable bonding in a variety of applications, including in the transportation, filter, electrical/electronics, wood processing, lightweight construction, and white goods sectors.
For sandwich elements and surface lamination, RAMPF has developed first-class PUR and hot-melt adhesive systems. These are used for facades and decorative elements, door, wall, and roof panels, composite building and construction elements, caravans and motorhomes, superstructures for commercial vehicles, and in transport vehicles (e.g. buses, trains).
RAMPF Production Systems, a leading provider of systems for processing one-, two-, and multi-component reaction resin systems and automation solutions, will be presenting, amongst others, the DR-CNC dispensing robot and the DC-CNC250 desktop dispensing ce
RAMPF Production Systems, a leading provider of systems for processing one-, two-, and multi-component reaction resin systems and automation solutions, will be presenting, amongst others, the DR-CNC dispensing robot and the DC-CNC250 desktop dispensing cell:
DR-CNC – the ideal solution for complex bonding, sealing, foaming, and casting requirements
With its separate material conditioning unit, the dispensing robot offers maximum flexibility for dynamic bonding, sealing, and casting. Variable X-Y-Z strokes also enable three-dimensional material application.
Up-to-the-minute Sinumerik 840D Solution Line control technology with OP08 operating panel means the DR-CNC combines the mixing and dispensing system with maintenance-free CNC linear axes. The result is flawless interplay between the dispensing process and axis motion sequences.
Flexible automation solutions are also possible – from manual through to automatic part loading. In addition, the modular control architecture allows for complete and effortless integration into production systems. Not only that, recipe management makes programming for different part types both simple and flexible.
Precision gear pumps near to the mixing system, servo-driven gear pumps for up to four components, and short hoses to the mixing system all unite to deliver high levels of dispensing accuracy.
A dual mixing system and rapid dispensing speeds significantly enhance the productivity of the produc-tion process.
DC-CNC250 desktop dispensing cell for high-precision dispensing of paste-like and abrasive materials
The desktop device has an integrated dispensing system and can be programmed for dispensing individual spots or lengths. The individual components are dispensed using a piston system designed to have an extremely long service life. This results in the highest levels of accuracy and long maintenance intervals.
The system can process any standard paste or adhesive that supports static mixing. It has a wide range of additional fit-out options, including a variety of material cartridge sizes and a table frame.
The advantages of the DC-CNC250 at a glance:
Compact design, but still flexible
- Desktop device with integrated controls and material supply
- Material supply from various cartridges separate from dispensing cell
- Good accessibility for maintenance work
High-precision dispensing of small volumes
- Processing of one- and two-component materials
- Processing of viscosities of approximately 100,000 - 700,000 mPa*s
- Static mixing system
- Fully adjustable mixing ratio from 100:100 - 100:1
- Dispensing volumes ? 5 mg / dispensing spot
- Processing of highly abrasive materials
Intelligent controls
- High-resolution 15" touch display with embedded PC.
- RAMPF process visualization
- User-friendly protection of insertion area with lifting door