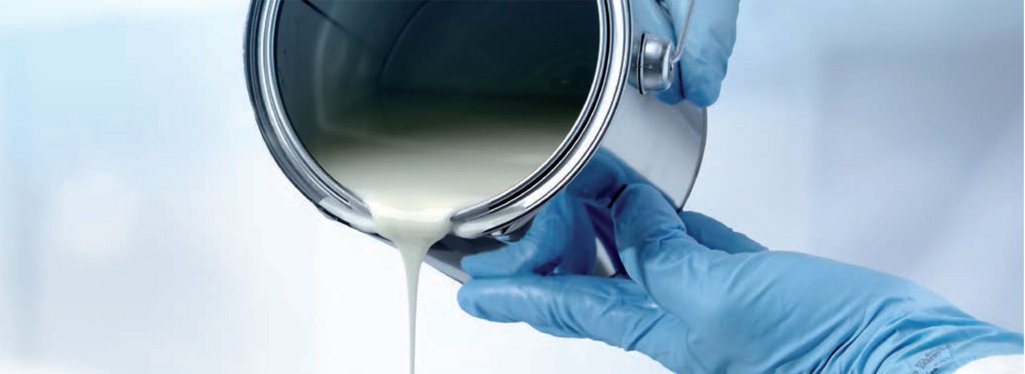
It’s All About Casting
09/12/19
Engineering Casting Resins
Casting methods with RAKU® TOOL casting resins.
This blog post provides information about the processing and benefits of
- Solid casting
- Face casting
Our short user videos tell you about the various products and provide a practical, step-by-step guide to how they are used.
Solid casting
The benefits:
- Castings are easy to finish / modify because only one material is used (monolith).
- It may be used with very complex geometries, where the lay-up process would be uneconomical.
- It's quick and easy to carry out in just one step.
- It can be used for both small and large components, depending on the chosen material.
How does solid casting work? What do you need to know?
- Mix the components well using the specified mixing ratio. When pouring and mixing the components, take care to avoid the formation of air pockets.
- You should therefore pour the material slowly and in a thin stream when casting. Evacuating the casting material considerably reduces the formation of air pockets.
- We recommend that you start pouring the casting material at the deepest point of the geometry. This way, the air in the geometry is displaced evenly by the casting resin during casting.
Face casting
The benefits
- It is ideal for dimensionally accurate castings because of the reactive material is distributed laminar, thus reducing shrinkage of the casting resin.
- It offers a low-cost means of producing larger components, as it uses less casting resin.
- Special surface properties can be achieved (from flexible to hard) by selecting an appropriate casting resin.
How does face casting work? What do you need to know?
- The first step is to produce an undersized displacement core. Depending on quality or cost considerations, displacement cores can be made of metal, wood or plastic. Plastic displacement cores can be produced by laying down a spacer film.
- Incorporating a gating system, feeder system, and ventilation holes into the displacement core as appropriate to its geometry.
- The gating should be located at the deepest point of the geometry. This way, the air in the geometry is displaced evenly by the casting resin during casting.
- When they sift through the feeders, they ensure they have a smaller cross section than the face of the cast. This will ensure the optimum performance of the feeders.
- When casting, try to ensure a constant and even stream of material so as to prevent air pockets. Do not stop the casting process until you see the casting resin coming out of the feeder;
- Tip: Evacuating the casting material before casting improves the end properties of the cured product.