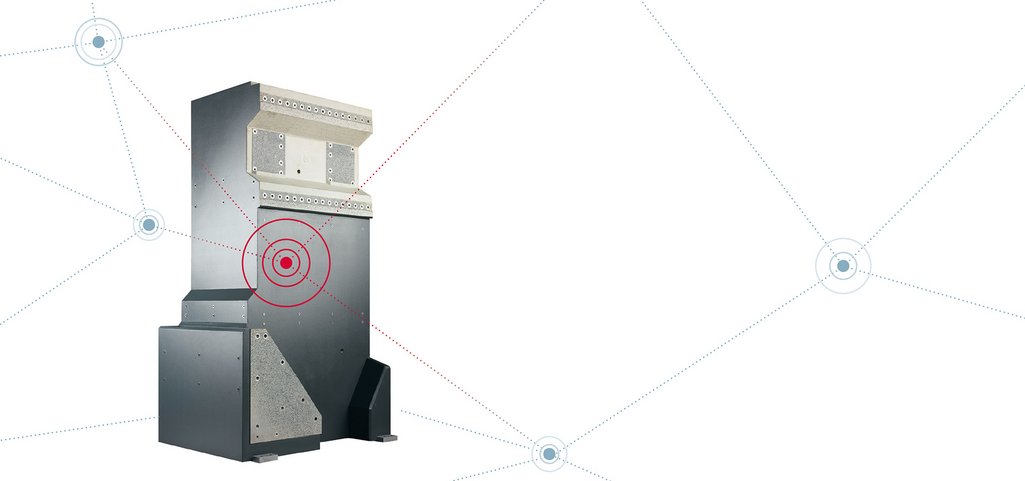
Industry 4.0 – when machine beds “have their say”
Ever faster, ever more dynamic, ever more precise – cutting-edge production technology has to meet requirements that are increasing rapidly. But it doesn’t end there. Machines can – no, must – now send their own status reports. This means they can optimize themselves, and thus the entire production process. All this thanks to Industry 4.0. Machine beds made using alternative materials such as mineral casting and ultra-high performance concrete provide a high-performance, low-vibration basis for this human-machine communication.
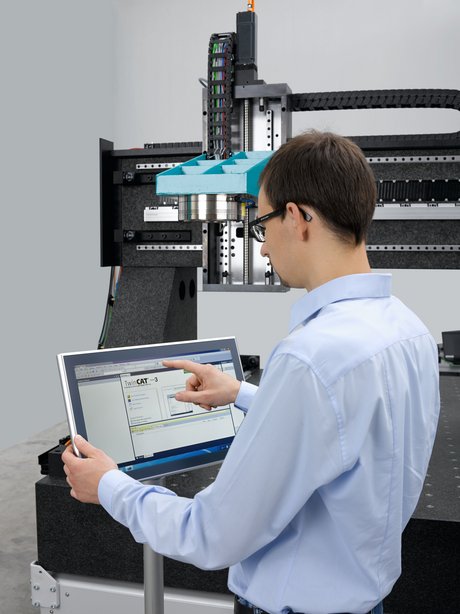
Combining communication and production in Industry 4.0
Digitization in industrial production is advancing at a breathtaking pace. Industry 4.0 – what scientists and politicians are calling the “fourth industrial revolution” – is in full swing.
In our everyday work, Industry 4.0 is primarily making its presence felt in the increasing communication between humans and machines. And the machines have a lot to say. Of course, Industry 4.0 is not about taking decision-making power away from humans. Instead, cutting-edge production technology supports them in their increasingly complex work. This includes, for example, automated monitoring for condition-based or preventive maintenance and improvements in effectiveness and productivity initiated and conducted by the machine itself.
In Industry 4.0, the machine operator therefore constantly receives updated information about the production process, while the machine itself ensures that the process runs perfectly, thus preventing or minimizing downtimes.
In Industry 4.0, intelligence starts with the machine bed
To achieve effective human-machine communication in Industry 4.0, every element in cutting-edge production technology must provide measuring data and information. This also applies to the machine bed, the foundation of the machine.
High-performance sensors capable of collecting and processing huge volumes of data in real time are required to make a machine bed “intelligent” for Industry 4.0. Alternative materials such as mineral casting and ultra-high performance concrete (UHPC) make it possible to integrate these sensors in efficient and cost-effective ways.
Machine beds can be cast at low temperatures (45°C – 60°C) by using alternative materials. “This in turn means sensors, actuators, and the associated leads can be cast directly into the machine bed,” explains Marc Dizdarevic, Head of Development at RAMPF Machine Systems, the world’s largest producer of mineral casting. “These kinds of sensors are being installed both in machine tools and increasingly in machinery for manufacturing electronics, solar modules, flat panels, and optics, in microproduction machines, and in machinery used in the textiles, wood processing, graphics, packaging, and laser industries. The objective: to keep the production process at the highest level.”
Industry 4.0? Yes. Vibrations? No thanks.
Of course, there are more advantages to using alternative machine bed materials than simply their suitability for integrating sensors for Industry 4.0. The special properties of these innovative materials offer attractive design options for improving dynamic machine performance.
Materials with high internal damping such as epoxy resin-bonded mineral casting (EPUMENT) and nano-technology-based UHPC (EPUDUR) have been used for decades in machine beds for highly dynamic production technology.
Industry 4.0 – discover the fourth industrial revolution
The digitization of industrial production processes is at the heart of Industry 4.0. This enables direct communication and cooperation between humans, machines, systems, logistics, and products, making it possible to manufacture products in more flexible, energy-efficient, resource-efficient, cost-effective, and customized ways. Industry 4.0 shapes the entire life cycle of a product – from concept and development to manufacture, utilization, and maintenance, all the way to recycling.