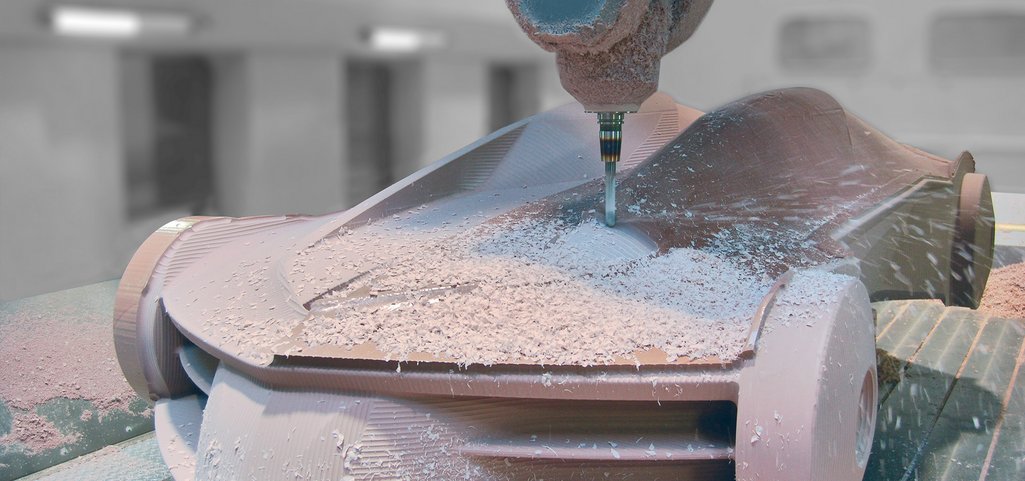
Mold engineering made in Germany – Close Contour Casting now also for NAFTA markets
Transatlantic technology transfer: The U.S. subsidiary RAMPF Group, Inc. now supplies the RAKU® TOOL Close Contour Casting technology for mold engineering developed and perfected by RAMPF Tooling Solutions in Germany. This means that high-quality models and molds can now also be manufactured in the NAFTA markets without the usual time-consuming process of modeling. This is a significant step forward for mold engineering overseas.
“With RAKU® TOOL Close Contour Casting we offer our customers in the aviation industry, automotive engineering, shipbuilding, motorsports, the rail industry, and the wind energy sector a unique technology that will considerably influence the manufacturing process for prototypes, cubing models, molds, and clamping fixtures,” says Mark Davidson, Head of Sales for Tooling Material at RAMPF Group, Inc.
Mold engineering with Close Contour Casting – the manufacturing process
1. First, RAKU® TOOL board material or a combination of board material and EPS (expanded polystyrene) are used to produce a lightweight, close-contour mold according to the customer’s CAD data. Once the mold has been milled, a release agent is applied. The mold is then filled using a special casting process with the aid of a two-component mixing and dispensing system.
2. After removal and curing, the ready-to-mill casting is sent for final processing to the customer…
Close Contour Casting in the United States
RAMPF Group, Inc. received support from Germany during the launch of Close Contour Casting technology. Mold engineering experts from RAMPF Tooling Solutions traveled to Wixom, Michigan, to install the two-component mixing and dispensing system and produce the inaugural casting. One of those experts was Jörg Hörz, Head of Production & Process Engineering at RAMPF Tooling Solutions: “Collaboration with our U.S. colleagues went very smoothly. We are extremely happy that they can now make full use of the potential that Close Contour Casting offers and make a real start with it in the NAFTA markets.”
Close Contour Casting now joins the RAKU® TOOL product portfolio of RAMPF Group, Inc., which already includes board materials for modeling and styling, Close Contour board material and pastes, as well as liquid systems that are long established in the NAFTA markets for model and tool engineering. Furthermore, a chemicals lab is currently being built at the company headquarters in Wixom, Michigan, that will enable RAMPF to offer its customers even better and faster support.
Close Contour Casting – the benefits for mold engineering:
- No time-consuming conventional modeling
- No bonding of board materials required
- No handling of liquid chemicals – customers can concentrate entirely on milling work
- Less manual finishing required, as the surface is seamless, smooth, and very dense thanks to the vacuum casting process