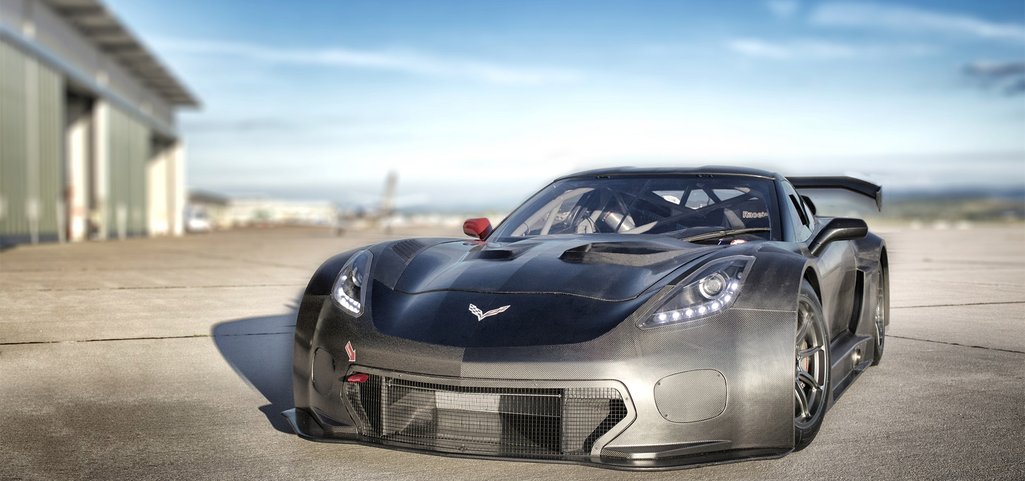
Composites on the edge – Callaway puts its faith in RAMPF
Carbon is everywhere in the new Corvette C7 GT3-R from Callaway Competition – also thanks to RAMPF Tooling Solutions and its lightweight construction solutions for composites. The Callaway Competition Corvette C7 GT3-R is ready for the new racing season and packed with heaps of power and hardly any weight.
It is not just the car’s fast lap times that catch the eye – so does its innovative design. This is where the RAKU® TOOL board and liquid materials from RAMPF Tooling Solutions, which have been developed specifically for the composites industry, have a vital role to play.
“This is the most beautiful car we have ever built,” say Giovanni Ciccone and Ernst Wöhr, owners of Callaway Competition. There is certainly no denying it. The new Corvette C7 GT3-R from the company based in Leingarten in the Baden-Württemberg region of Germany is a real feast for the eyes. It exudes power, but also boasts elegant contours and sophisticated aerodynamics. And everywhere there is carbon.
Improving a winner
Callaway Competition has been racing for over 25 years, and is the longest-serving team in the ADAC GT Masters, the prestigious race series for GT3-class sports cars. There has never been a race in this series without a Callaway Corvette on the grid. With 23 race wins, the Callaway Corvette Z06.R GT3 is the most successful racing car in the history of the ADAC GT Masters.
For the new C7 GT3-R Corvette only the chassis and the up to 600 HP, water-cooled, 6.2-liter V8 engine were taken aboard from the series model. Development of the vehicle – done completely in-house – began with CAD work on the technically-relevant parts in mid-2014. The vehicle design was finalized by the end of the year, and construction began in Leingarten in spring 2015.
The molds for the racing car were milled directly based on CAD data. RAMPF Tooling Solutions delivered high-quality RAKU® TOOL board materials that were used to create molds for producing various composite parts for the C7 GT3-R. RAKU® TOOL resin infusion was used for those parts that were not manufactured in prepreg.
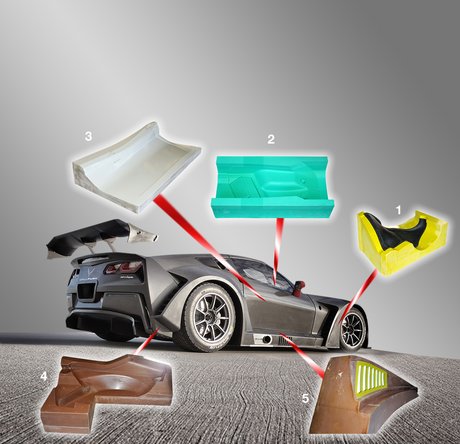
1. Die Bremsluftführung wurde aus Formen mit Werkzeugblockmaterial RAKU® TOOL WB-1404 hergestellt. Bei der Produktion der Kohlefaserteile kam das Epoxid-Infusion-System RAKU® TOOL EI-2500 / EH-2970 zum Einsatz.
2. Die Mittelkonsole wurde aus Formen mit Epoxid Werkzeugblockmaterial RAKU® TOOL WB-0700 hergestellt.
3. Die Türaußenhaut wurde aus Formen mit Werkzeugblockmaterial RAKU® TOOL WB-0801 hergestellt.
4. Der hintere Kotflügel wurde aus Formen mit Modellblockmaterial RAKU® TOOL MB-0600 hergestellt.
5. Der vordere Kotflügel wurde aus Formen mit Werkzeugblockmaterial RAKU® TOOL WB-1404 und dem Modellbaublockmaterial MB-0600 hergestellt.
Complete solution for the composites industry
“RAKU® TOOL WB-0691 and WB-0700 are particularly suited for lay-up tools, vacuum forming molds, and for processing prepregs,” explains Marcus Vohrer, Head of Application Engineering at RAMPF Tooling Solutions. “RAKU® TOOL WB-1404 molds were used to manufacture carbon fiber parts with EI-2500 / EH-2970 resin infusion. The benefits this provides are an outstanding surface on the resin-infusion parts, excellent fit accuracies, and no damage to the molds during demolding.”
RAMPF Tooling Solutions offers a comprehensive range of liquid, paste, and board materials specifically for the composites industry. This includes epoxy and polyurethane systems, and ensures consistent product quality with excellent mechanical end properties. “Incorporating these new plastics and technologies helps extract the greatest possible benefit from lightweight construction using composites,” says Heinz Horbanski, Managing Director of the international modeling and mold engineering specialists from Grafenberg, near Metzingen.
Success factor composites – always a front spoiler’s length ahead
Without a doubt, the new Corvette C7 GT3-R is a masterpiece. “As a private team, projects such as this present a particular challenge, as we cannot call on the financial and staffing resources of a large automobile plant. However, thanks to the tireless efforts of our staff and technology partners, we have been able to finish the vehicle in a comparatively short space of time,” says Ernst Wöhr.
The central contact for the composite manufacturing process was Esterlössl GmbH, from Rutesheim. The carbon-fiber components in the prepreg process were manufactured by Murr-based ubc GmbH and Brebeck Composites GmbH in the Czech Republic, while Schäfer Modell- und Formenbau GmbH and Kegelmann Technik GmbH from Rodgau-Jügesheim were responsible for doors, interior fittings, and the front hoods.
Incidentally, it is not only racing enthusiasts in Germany who will have the pleasure of seeing the C7 GT3-R in action on the track. The car meets the specifications and safety requirements of the FIA, the world governing body for automobiles and motor sport, and can therefore be used in races around the world.