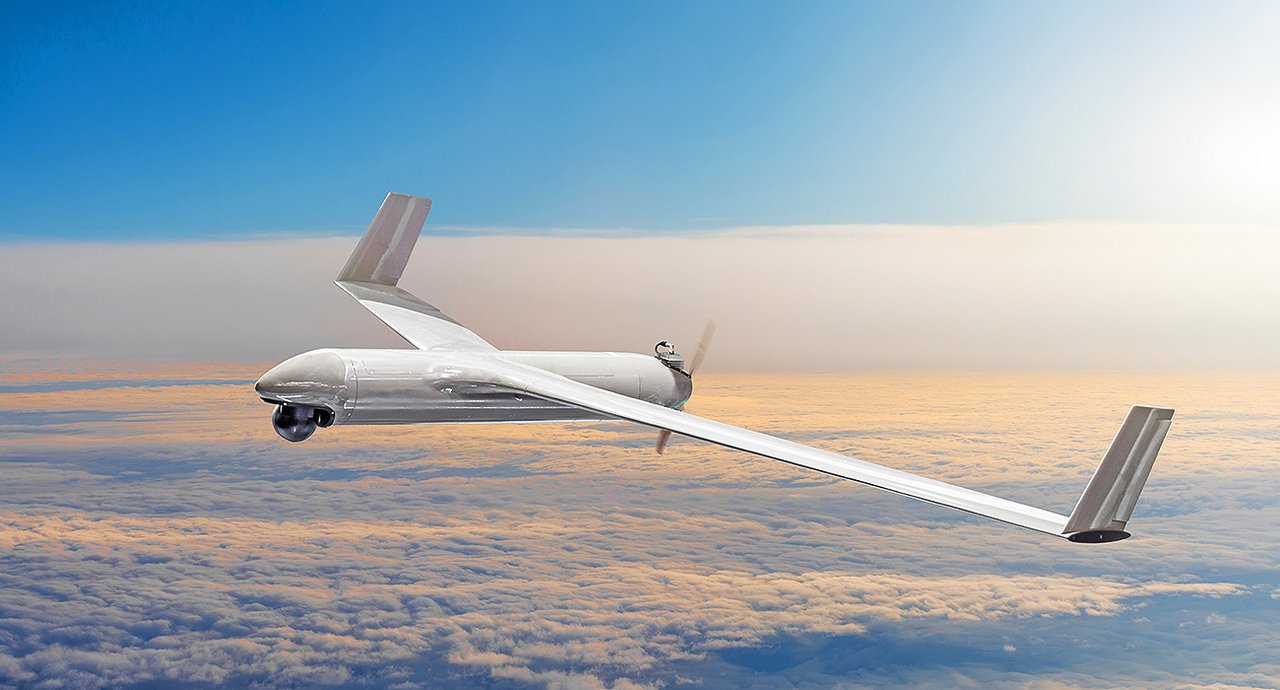
RAMPF: One-Stop Solution for UAV Composite Manufacturing
The RAMPF Group is showcasing high-performance tooling materials and groundbreaking engineering solutions for the rapid and cost-effective manufacture of composite parts in the UAV industry at Xponential in Houston, TX, from May 20 to 22 – Booth 2020.
Key Facts
- Through advanced tooling materials and innovative engineering solutions, the RAMPF Group companies accelerate composite manufacturing while significantly reducing costs.
- RAMPF Group, Inc., based in Wixom, MI, USA, offers high-performance tooling boards, Close Contour Castings, and liquid resin systems with outstanding mechanical and chemical properties.
- RAMPF Composite Solutions based in Burlington, Ontario, Canada, designs and manufactures advanced lightweight components, maximizing the potential of composite technology from early development and low-volume production to full-scale series manufacturing.
- RAKU® TOOL tooling boards based on epoxy exhibit outstanding mechanical properties, finest surface structures, and high dimensional stability. The boards are easy and quick to machine and compatible with all industry-standard prepregs, release agents, and paints.
- RAKU® TOOL Close Contour Castings made from polyurethane are delivered as a ready-to-machine monolithic casting, free of bonding lines and in a near-net shape. This significantly reduces both milling time and material waste.
- RAKU® structural resins enable low-temperature processing without the need for expensive equipment. These scalable materials reduce prototyping lead times and costs by up to 30 percent, while meeting FST standards including FAR 23.1193, 25.853, and 25.855.
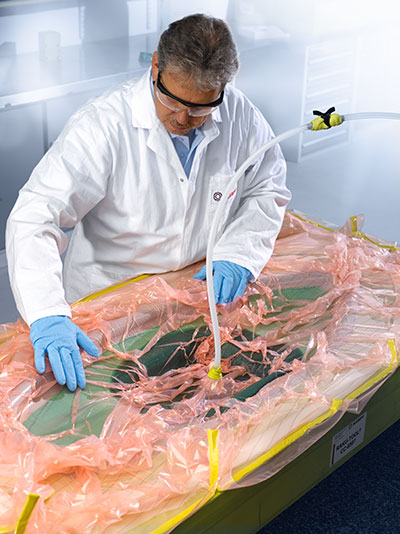
RAMPF Composite Solutions specializes in the design and manufacture of advanced lightweight composite parts for the UAV industry, including rotor blades, battery enclosures, fairings, and cowlings. The company’s experts harness the full potential of composite technology across all stages – from early development and low-volume runs to full-scale production.
The groundbreaking approach combines:
- Low-cost tooling and fixtures for outstanding mechanical properties, ensuring high-quality production at reduced costs.
- High-performance structural resins for effective and fast infusion, enhancing the efficiency of the manufacturing process.
- Tailored Fiber Placement (TFP) technology for optimized structural components with maximum speed and accuracy.
- Vacuum Assisted Resin Transfer Molding (VARTM) for low-cost component production.
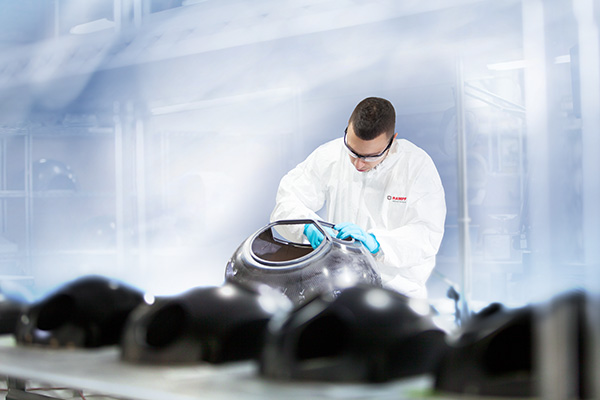