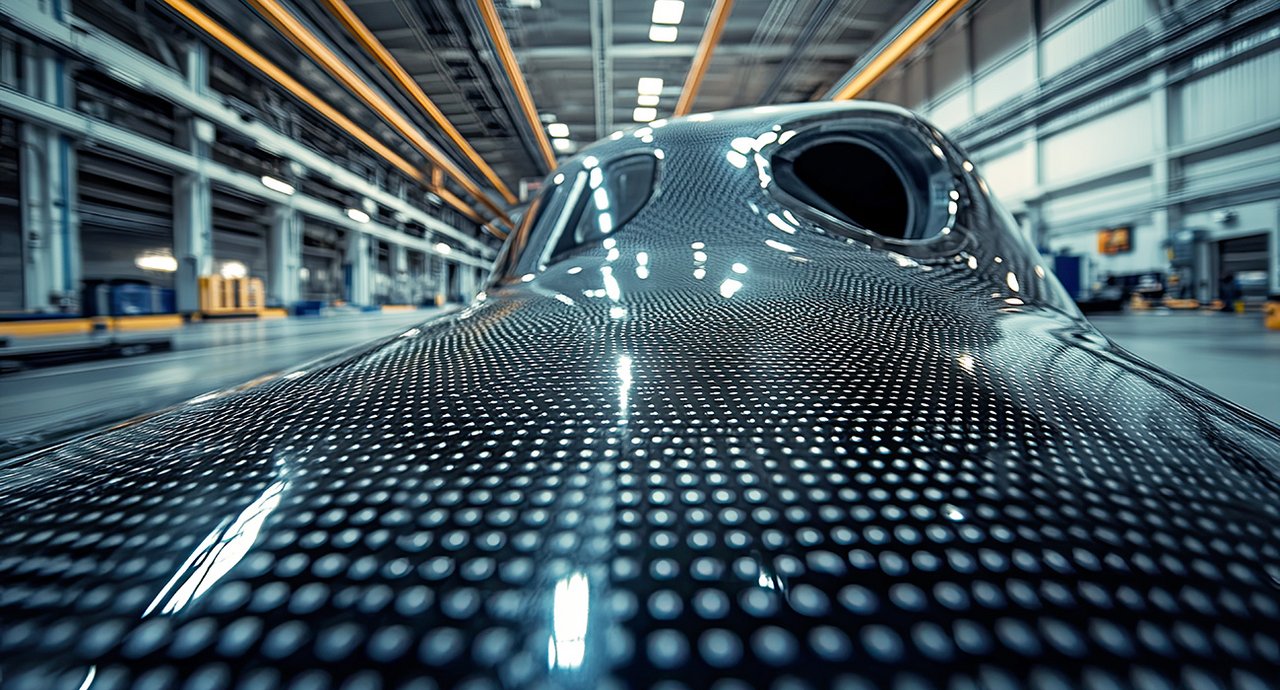
Accelerating Defense Innovation – Fast & Cost-Efficient Composite Manufacturing by RAMPF
RAMPF is driving the rapid development and cost-efficient production of high-quality composite parts for the defense sector with its comprehensive portfolio of tooling boards, liquid systems, and cutting-edge engineering expertise.
Key Takeaways
- The international RAMPF Group specializes in high-performance materials and advanced engineering solutions for manufacturing high-quality composite parts for the defense sector, including aerospace, marine, and mobility applications.
- RAMPF Advanced Polymers offers precision, performance, and efficiency in composite manufacturing with tooling materials such as boards, near-net-shape castings, and Close Contour pastes engineered for molds and models with superior dimensional stability, part accuracy, thermal resistance, exceptional surface quality, and cost-saving processing. A broad portfolio of liquid systems facilitates precise tailoring of final part performance to meet any requirement.
- RAMPF Composite Solutions has engineered a one-stop solution for manufacturing complex composite parts, delivering up to 30 percent cost savings across low-volume production, early-stage development, and series manufacturing.
Advancing technologies and the need for rapid deployment are accelerating demand for high-performance and lightweight solutions in the defense industry. This development is being propelled by cutting-edge composite materials, combining outstanding strength-to-weight ratios with durability and resistance to harsh environments – ensuring long-term performance and reliability of military equipment.
From aircraft, drones, and flight simulators to ships, land vehicles, and impact and structural testing equipment – tooling materials, liquid systems, and engineering competence from RAMPF ensure maximum speed, performance, and cost-efficiency for composite part manufacturing.
Boards, Close Contour materials, and liquid systems for model and mold engineering by RAMPF Advanced Polymers
Model and mold engineering materials are crucial for the composite industry, allowing for the precise fabrication of high-quality parts. RAMPF Advanced Polymers has an encompassing portfolio of tooling boards, Close Contour materials, and liquid systems specially developed for composite manufacturing processes such as Autoclave, Vacuum Bagging/Prepreg (Out of Autoclave), Resin Transfer Molding (RTM), Resin Infusion, Wet Compression Molding, Vacuum Bagging/Wet Lay-Up, and Hand/Wet Lay-Up.
RAKU® TOOL Epoxy Boards
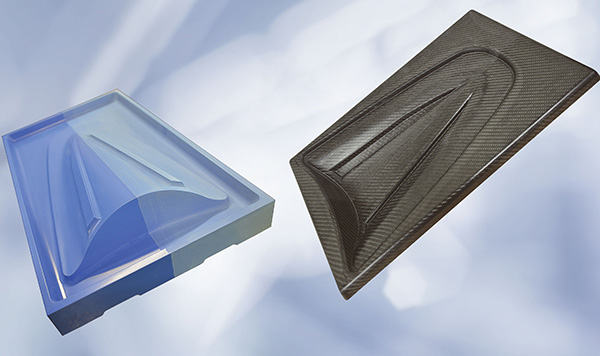
RAMPF’s high-performance board materials ensure precise model and mold production to enable the manufacture of composite parts with complex geometries and exceptional surface quality. The epoxy boards RAKU® TOOL WB-0890, RAKU® TOOL WB-0700, and RAKU® TOOL WB-0691 are specially developed for the composites industry. The benefits:
- Superior surface, minimizing sealer consumption and finishing effort
- Dimensionally stable
- Good temperature resistance
- Easy to mill
- Compatible with all standard sealers and release agents
- Adhesive and repair package tailored to heat resistance and hardness of boards
- Short processing times
Close Contour Castings
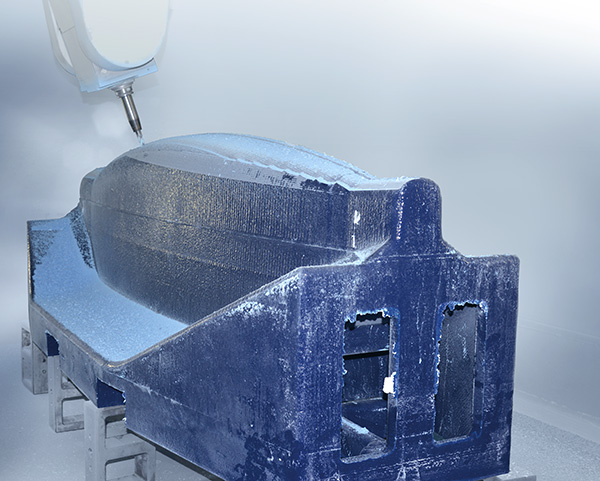
RAKU® TOOL Close Contour Castings are semi-finished, ready-to-mill materials provided as three-dimensional castings matching the final contour of the mold. This innovative technology enables the cost-efficient and resource-saving production of highly dimensionally stable models and molds. The benefits:
- Monolithic, seamless parts without bonding lines
- Fine and homogeneous surface quality with outstanding surface quality
- Excellent dimensional stability
- Reduction of milling time and waste
Close Contour Pastes
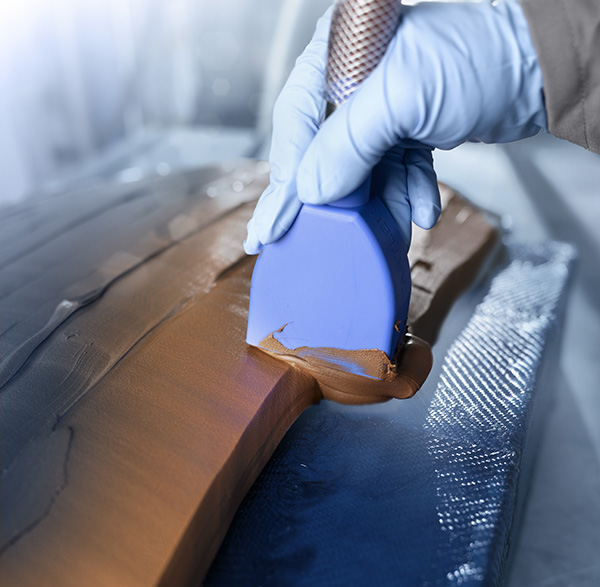
RAKU® TOOL Close Contour Pastes, two-component epoxy systems, are processed and applied via mixing and dispensing machines. The thixotropic, easy-to-process materials deliver dimensionally stable, seamless models and molds. The benefits:
- Very fine, homogeneous, and seamless surface
- Cost-efficient model construction thanks to optimized substructures
- Easy and fast milling with less waste due to close contour shape
- Good dimensional stability
- Processing without slump on vertical surfaces
- Low exotherm
- Quick machinability
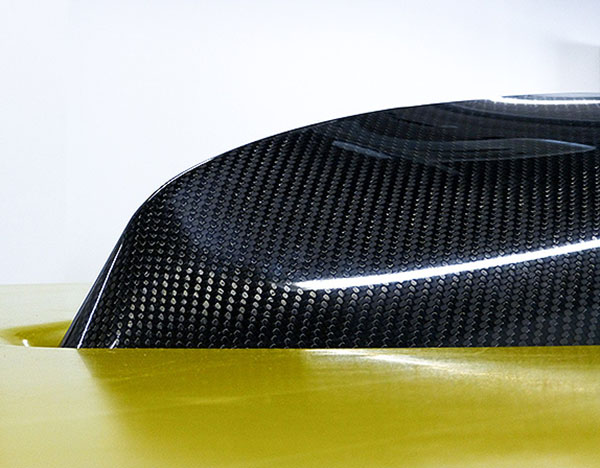
RTM, infusion and epoxy laminating systems, as well as gelcoats ensure a strong bond between fibers and resin, enhancing the mechanical performance, durability, and surface quality of the final composite part. The benefits:
- RTM and infusion systems – Low viscosity; no offgassing under vacuum; excellent wetting and flow properties; suitable for high-temperature applications
- Laminating systems – High mechanical properties with room temperature curing; excellent wetting properties; pot life and curing times adjustable via hardeners; outstanding compatibility with fibers, fabrics, and fillers
- Gelcoat systems – Sandable and polishable; abrasion and chemical resistant; high-temperature applications
Denny Föhn, Director Business Center Tooling & Modeling at RAMPF Advanced Polymers:
RAMPF Advanced Polymers delivers precision, performance, and efficiency in composite manufacturing with a complete range of tooling boards, Close Contour materials, and liquid systems. Our materials are engineered for superior dimensional stability, part accuracy, thermal resistance, exceptional surface quality, and cost-saving processing.
One-Stop Solution for Complex Composite Part Manufacturing by RAMPF Composite Solutions
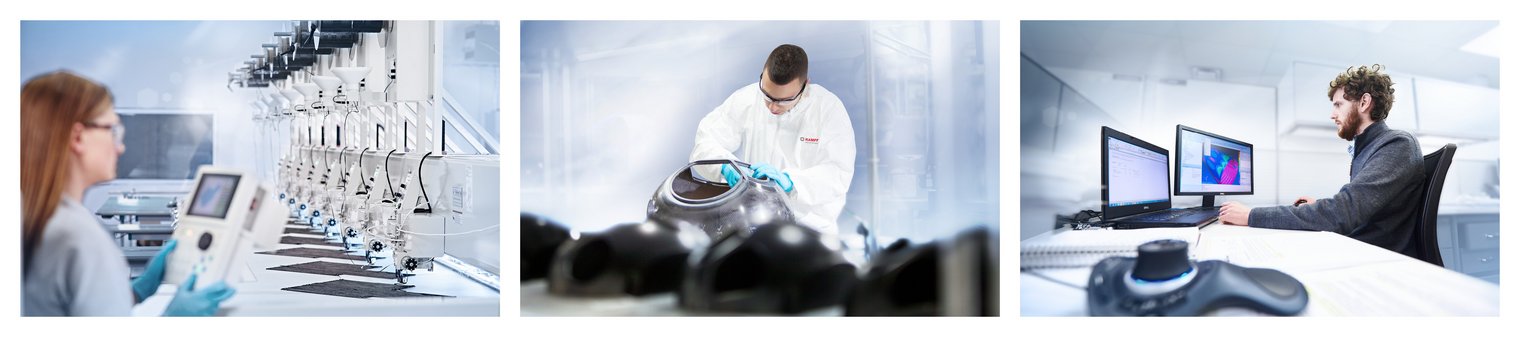
RAMPF Composite Solutions is driving innovation in the defense industry with its one-stop solution for the quick and cost-efficient development and manufacture of complex composite parts.
The company’s experts leverage the full potential of composite technology across various stages, including low-volume production, early product development, and series production. The groundbreaking approach combines:
- Low-cost tooling and fixtures for outstanding mechanical properties, ensuring high-quality production at reduced costs.
- High-performance structural resins for effective and fast infusion, enhancing manufacturing efficiency.
- Tailored Fiber Placement (TFP) technology for optimized structural components with maximum speed and accuracy.
- Vacuum Assisted Resin Transfer Molding (VARTM) for low-cost component production.
RAMPF Composite Solutions delivers fast, innovative solutions that integrate material qualification, automated manufacturing, and quality assurance for components and subsystems. From the very beginning, experienced engineering experts engage in every step of the process, considering all aspects of design, development, and manufacturing. Their holistic approach ensures not only technical excellence but also compliance with safety standards and qualification requirements.
Advanced Resin Infusion Technology
RAMPF Composite Solutions’ resin infusion technology offers substantial cost savings and enhanced production efficiency compared to traditional prepreg-based methods. Developed entirely in-house, the process meets the rigorous standards of industries such as aerospace, while supporting scalable, high-volume manufacturing.
Especially well-suited for complex, high-performance components, this advanced technology delivers an ideal balance of strength, weight, and cost-efficiency. The benefits:
- Up to 30 percent cost savings – High-quality components produced at a fraction of traditional prepreg costs.
- Sustainable manufacturing – No refrigeration or autoclaves, drastically reducing energy consumption and carbon footprint.
- Enhanced production efficiency – Faster lead times and lower costs through integrated manufacturing processes.
State-of-the-Art Infrastructure
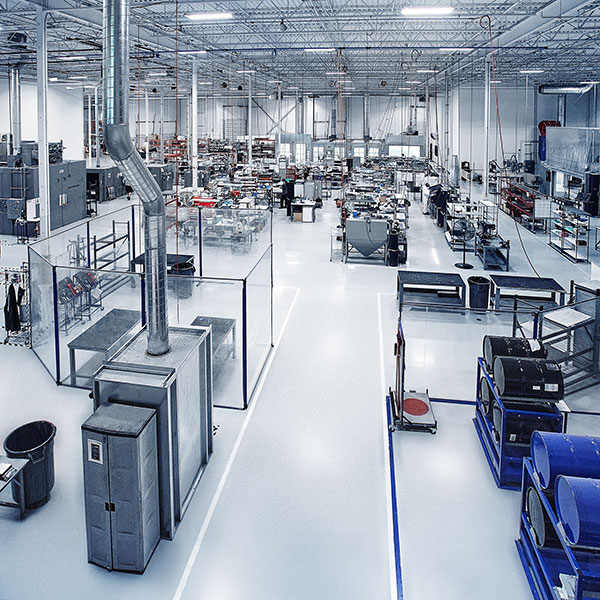
RAMPF Composite Solutions’ high-tech, 74,000-square-foot facility in Burlington, Ontario, Canada, is designed to optimize every stage of the composite manufacturing process. Facility features include:
- Temperature-controlled lamination room
- AI-driven ply cutting system
- Automated resin mixing and dispensing
- Large curing ovens
- Advanced CNC machines
- Metallic plating
- Robotic sanding
- Large paint booths
- Destructive and non-destructive testing equipment
- 3D printer for thermoplastic printing
Max Schultes, Chief Technology Officer at RAMPF Composite Solutions:
We design and manufacture some of the world’s most advanced lightweight composite products. Our fully integrated, in-house composite manufacturing solution significantly cuts costs and lead times. By streamlining the entire process – from design to final part – we empower our customers to accelerate deployment in even the most demanding defense applications.