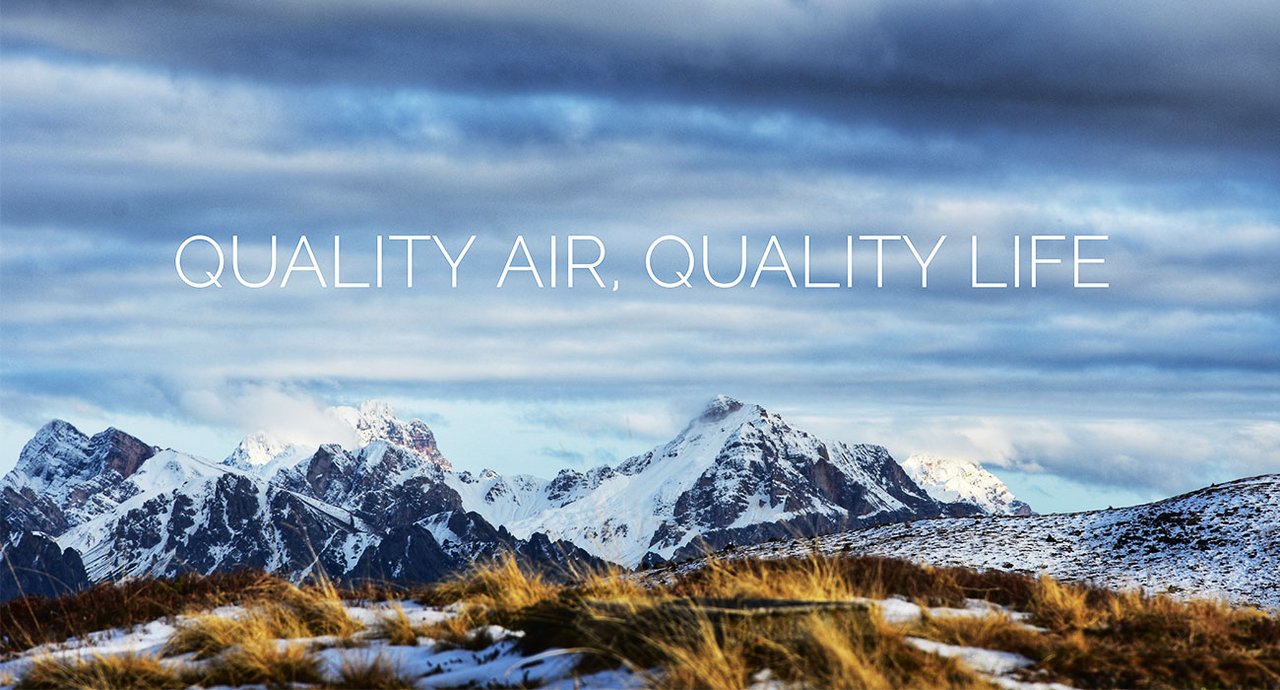
Optimum Air Quality – Optimum Production Efficiency
Across the globe, WEGER air handling units (HVAC) ensure clean air and ideal climate conditions for everything from shopping malls and hospitals to farms. To manufacture its highly complex system solutions, the company uses automated production processes and an antibacterial polyurethane foam gasket from RAMPF.
Covering a total area of more than 65,000 square meters and attracting millions of visitors every year, the Mall of Switzerland in Ebikon is a large, ultra-modern shopping mall and leisure complex with over 80 stores and twelve restaurants. From the sweltering heat of summer to the icy depths of winter, a high-performance WEGER ventilation system always ensures a pleasant environment for shoppers.
WEGER supplied a total of 17 air handling units for the Mall of Switzerland in various sizes and for different purposes, including stores, an indoor children’s play area, kitchens, and parking lots. The total volume of air handled by these units is 520,000 m³/h. By way of comparison, a person’s typical “air consumption” is around 1 m³/h.
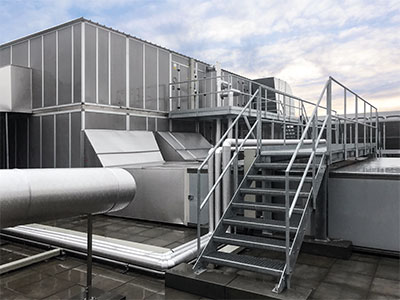
Founded in 1977 and based in Kiens, in Italy’s South Tyrol region, the family company has long since established itself as a renowned supplier of complete air handling and climate control systems. Its portfolio covers HVAC units and the associated housings, along with heat exchanger connection kits and control systems. Customers worldwide – from the above-mentioned shopping mall to hospitals, offices, educational establishments, and offshore platforms – make use of this comprehensive range.
Customized mass production
The units developed by WEGER are tailored to the needs of customers from various sectors, based on the concept of customized mass production, i.e. the maximum possible number of processes are standardized and automated. RAMPF Production Systems also makes an important contribution to this with its DR-CNC dispensing robot, including several digitalized processes.
Using cutting-edge control technology, the DR-CNC combines the mixing and dispensing system with maintenance-free CNC linear axes. This ensures perfect interplay between the dispensing process and motion sequences. Adaptable X-Y-Z axis strokes provide excellent flexibility, while the modular control structure makes it easy to integrate the dispensing robot into existing production lines.
Upping the pace with FlexSpeed
The speed-dependent dispensing technology FlexSpeed developed by RAMPF Production Systems guarantees for maximum dispensing speeds. Whereas dispensing robots normally operate at constant application speeds, FlexSpeed technology enables them to reach up to 40 m/min. in a straight line, while braking down to 20 m/min. in a controlled way just before corners and curves. This cuts throughput times for sealing, foaming, and bonding processes in series production by up to 50 percent. RAMPF Production Systems’ dynamic MS-C100 mixing system applies the two-component polyurethane foam to the thermal panels with high precision.
What’s more, the necessary information about the geometry of the component and gasket is transferred to the system in advance by scanning a QR code for details of the part sizes. An OPC-UA connection to the WEGER production system enables real-time process monitoring.
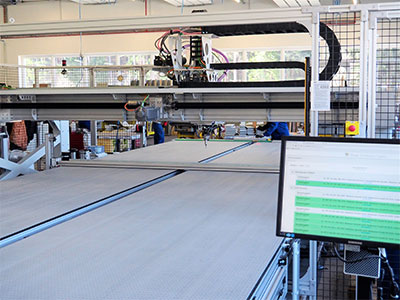
RAKU® PUR 32-3294-2 – maximum sealing quality and optimum physical properties
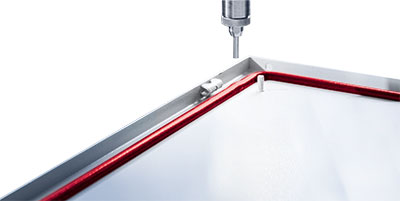
WEGER uses a RAKU® PUR 32-3294-2 antibacterial foam gasket from RAMPF Polymer Solutions to seal the thermal panels. Certified to DIN EN ISO 846 (11/2020) and VDI 6022, these gaskets ensure no mildew, yeasts, or bacteria can form on the material.
Used in both indoor and outdoor applications, the two-component polyurethane system is suitable for flat surfaces and grooves alike. Impressive features include:
- Top sealing quality in terms of IP requirements
- Very low levels of compression set
- Very low density, which minimizes the amount of material used
- Flexible adjustment of Shore hardness (Shore 00: 40-70)
- Extremely low water absorption
- Very fast cycle and handling times thanks to a very short tack-free time (RAKU® Speed technology)
Thomas Weger, Development Engineer at WEGER:
The machinery design has been adapted to our specific wishes and Industry 4.0 requirements. We are impressed by the flexibility and the excellent service we received during the collaboration, both at our plant in Kiens and in Hungary.
Stefan Roth, Regional Sales Manager at RAMPF Production Systems:
The modular, highly automated production operation at WEGER is a prime example of how to manufacture customized products of the highest quality based on mass production. We are making a key contribution to this with our approach of developing both the mixing and dispensing technology and further automation process steps. What’s more, we are able to harness synergy effects within the RAMPF Group by using the antibacterial polyurethane foam gaskets of our sister company RAMPF Polymer Solutions.