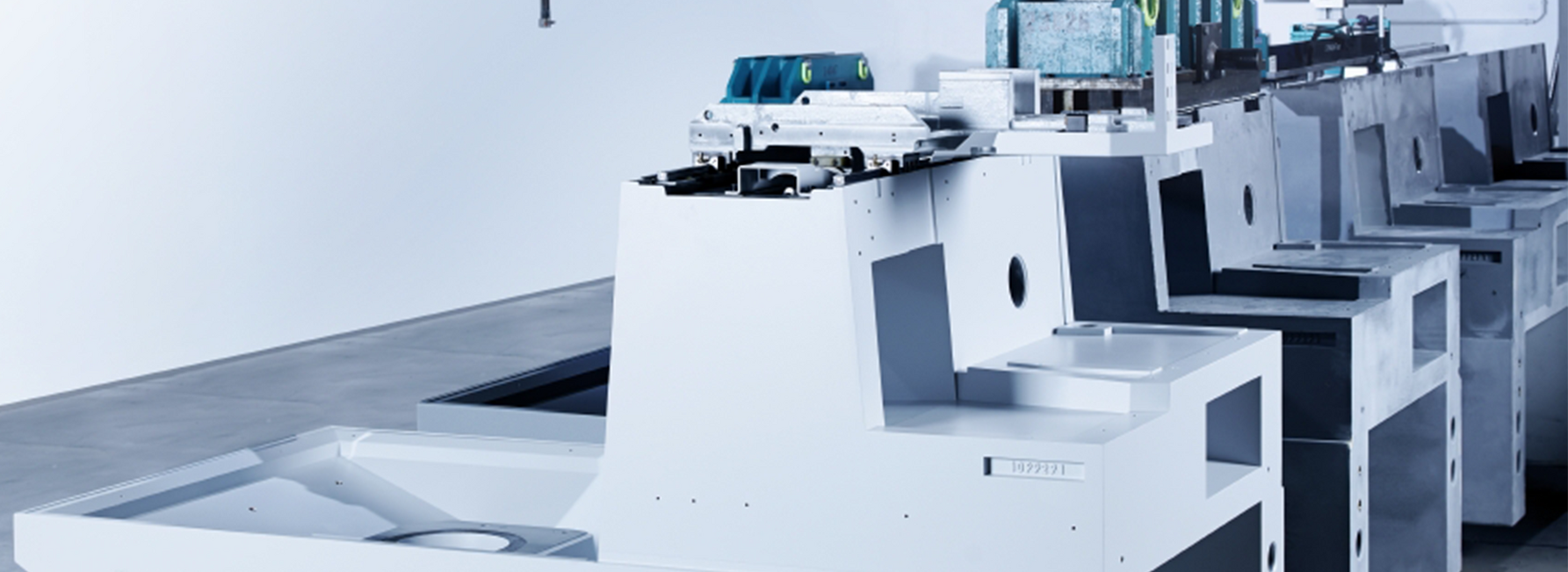
Exceptional performance and vibration damping
Protecting the climate and the environment does not run contrary to either economic or technical interests. In fact, climate-friendly solutions are the economic basis for a sustainable future. The order of the day is to cut environmentally damaging emissions and, where possible, to avoid them completely.
After all, these emissions will be key to pricing policy and the competitiveness of products in the future. We can only reduce emissions when we know what is causing them. RAMPF Machine Systems therefore tasked an independent agency with examining EPUMENT® mineral casting and ascertaining this material’s carbon footprint.
At approximately 360 kg CO2e per metric ton, the superiority of RAMPF mineral casting to other machine bed materials is abundantly clear. For example, the emissions per metric ton of mineral casting are 4.5 times lower than those per metric ton of gray cast iron!
Proportion of emissions and targeted optimization
The diagram below shows that the actual manufacturing process for EPUMENT® mineral casting only accounts for just under 4 percent of the total emissions – the procurement of materials accounts for the remaining 96 percent.
This information is hugely important to RAMPF. It tells us how we can further minimize the carbon footprint of our mineral casting and make this material even more sustainable.
Accordingly, our developers are working on obtaining raw materials from renewable resources. Recovering raw materials from recycled materials is also an important focal point, and having our very own recycling company – RAMPF Eco Solutions in Pirmasens – means RAMPF is very well placed to do so.
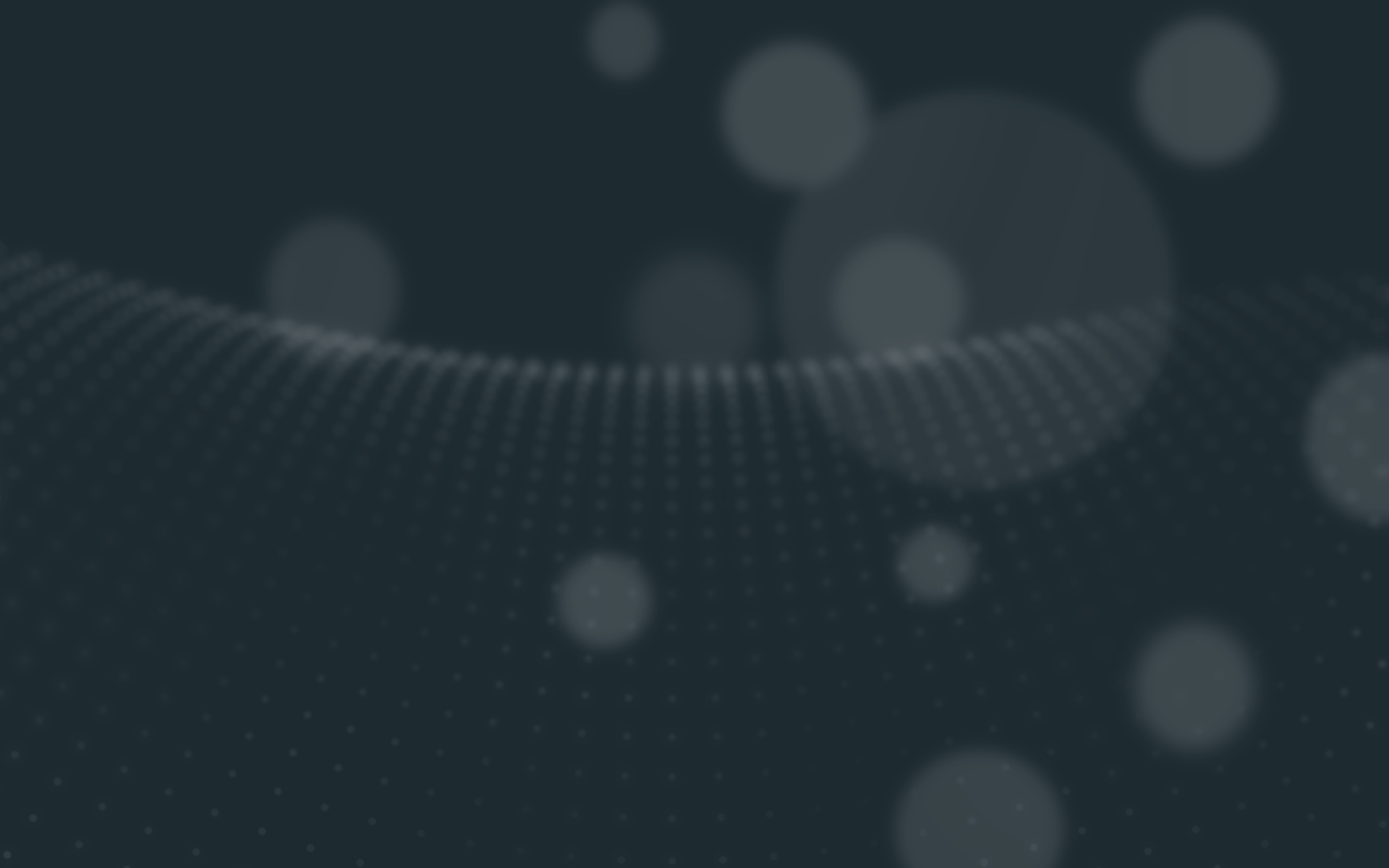
Advantages of mineral casting
- Consists of over 90 percent naturally occurring minerals and stones
- Disposed of as normal construction waste and can be reused as a recycled material in construction
- Powdered limestone provides a natural fine filler as an alternative to fly ash from the combustion of coal
- RAMPF replication technology saves on transport operations and energy costs for finishing machines
EPUMENT® mineral casting is a good alternative to metallic materials. It can significantly reduce the carbon footprint of your machine, while also improving its technical features.
By switching to mineral casting from RAMPF, you are making an important contribution to protecting our environment and putting yourself in an excellent position to take further measures relating to climate-neutral production.
It goes without saying that our development team will be more than happy to help you with the design and the switchover from your current setup.