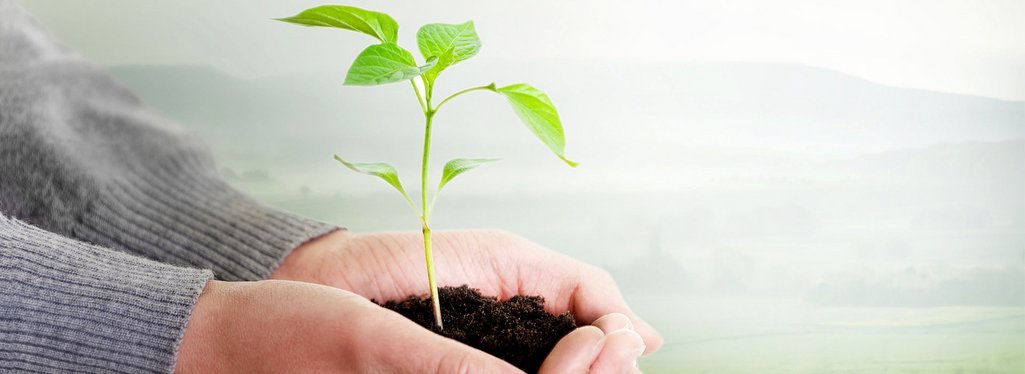
„It is all about upcycling“
RAMPF Eco Solutions is a true pioneer of polyurethane recycling. CEO Matthias Rampf and Marco Werth, Director of Sales & Marketing, explain how the company extracts high-quality recycling polyols from used mattresses, furniture, or car seats – and why this brings customers far more than just economic benefits.
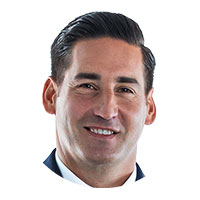
RAMPF Eco Solutions is an expert in chemical solutions for the production of high-quality recycled polyols. What does this encompass?
Matthias Rampf: Put simply, we recycle post-consumer residues such as used mattresses, furniture, car seats, motorcycle seats, fitness and leisure items, and insulation materials. We also process industrial residues such as production waste, scrap, or entire products at the end of their life cycle. Adding a little more chemistry to the explanation – we are a specialist for the recycling of polyurethane residues.
Polyurethane, PU, is a versatile plastic that has a wide variety of material properties and is therefore used in many industries and applications. In addition to thermal recycling, which does not really reflect the current zeitgeist, PU can be recycled mechanically and chemically. In mechanical recycling, the material is reused in its polymer form, but the potential applications are comparatively limited. That is why RAMPF Eco Solutions dedicated itself to chemical recycling more than three decades ago.
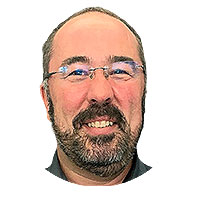
Marco Werth: In our process, PU is broken down into its basic chemical components and processed in such a way that the products, so-called polyols, can be reused as a secondary resource in the chemical industry. The aim is that the recycled polyols recovered this way are at the very least comparable with the polyols otherwise obtained from fossil raw materials, both in terms of quality and technical properties, and that they can therefore be used directly in the production process for new products. This creates a cycle that combines economic and ecological advantages.
The important thing is – this is upcycling, not downcycling. A decisive advantage for our customers is that our recycled polyols can be tailored to their respective applications. For example, producers of tooling boards or molded parts can improve the compressive strength of insulating foams, the chemical stability of casting compounds, or the compatibility of polyurethane systems by adding our recycling polyols.
Are there further advantages of recycling polyols?
Marco Werth: The fundamental prerequisite for the use of recycling polyols is that they are of the highest quality and tailored to the applications of our customers. The chemical solutions we develop guarantee exactly that. By using recycled polyols, our customers make themselves independent of fluctuating crude oil prices and reduce their disposal costs. With regard to the current dynamics on the raw materials market, many players are also seeing that the decoupling or diversification of raw material sources achieved through our recycling polyols is a tangible entrepreneurial and strategic competitive advantage.
Matthias Rampf: Another very important advantage is the reputational gain for companies that use recycling solutions. As FSK CEO Klaus Junginger emphasized in his interview – sustainability, environmental protection, recycling, and recovery play an increasingly important role in both politics and society. This is also mirrored in the new generation of users, tinkerers, problem solvers, and consumers who are more than aware of the problems surrounding climate protection and synthetic waste in natural ecosystems. We are currently living in the midst of a comprehensive, global change process that is fundamentally altering the perspective on the topic of recycling in society.
Can those polymers also be recycled that play a significantly larger role on the market than polyurethane?
Marco Werth: Yes, other polymers are also suitable for chemical recycling. RAMPF Eco Solutions developed a process for the chemical recycling of polyethylene terephthalate, better known as PET, back in 1999 together with the German Society for Circular Economy and Raw Materials (DKR). The recycling polyols generated here are particularly suitable for the production of rigid foams. We also use polyesters such as polylactides, polycarbonate, and polyhydroxyalkanoates as raw material sources, as well as renewable or bio-based raw materials such as rapeseed oil.
Since we see great potential in renewable raw materials, we have taken part in numerous international research projects in this field, for example on the recycling of lignin, a waste material from the processing of cellulose in paper manufacturing.
RAMPF Eco Solutions also develops and constructs multifunctional recycling plants for polyol production. Who are your customers?
Marco Werth: Companies that have a high volume of PU residues can produce high-quality recycled polyols on site with their own recycling plant, thereby saving costs and protecting the environment. They can then use these polyols in their production process. With our multifunctional pants, as the term multifunctional suggests, polyols can also be produced based on PET as well as phthalic anhydride or polyisocyanurate. For the planning and manufacture of the plants, we cooperate with leading industrial plant construction companies. This offer is profitable from both an economic and an ecological point of view. We have sold plants all around the globe, including Dubai.
Can Design for Recyclability also be implemented for PU products? Is RAMPF Eco Solutions supporting this as a development partner?
Matthias Rampf: Design for Recyclability is a very interesting approach that is not initially limited to the chemical industry; it is more about the idea of designing products at an early stage of development so that they can be recycled. If recyclability is a requirement for the product, then it is also relevant for the raw materials in the upstream value chain. This topic is high on our agenda, not least because it outlines the understanding of recycling as we have been living it for almost thirty years.
Marco Werth: For PU-based products, we see great potential in terms of Design for Recyclability. As a thermoset material and unlike thermoplastics, PU can usually only be recycled with great effort. From a technical point of view, it is essentially a question of the targeted splitting of polymer chains. This is closely related to our day-to-day business, so we are well positioned here already.
ERROR: Content Element with uid "52506" and type "textBesideImage" has no rendering definition!