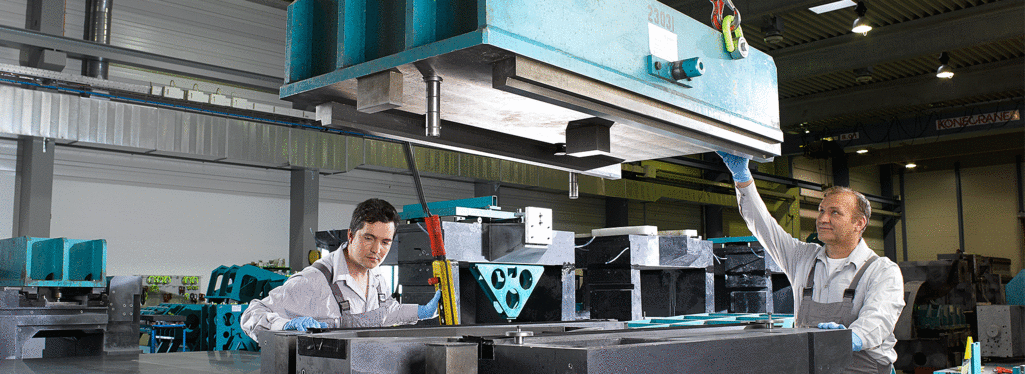
How to (2) – Mineral Casting Components with Maximum Precision
Machine Tools and production machines in the semiconductor, laser, medical, and packaging industries carry out high-precision processes. For this, the individual components of the machine must be perfectly assembled with the machine bed or frame component. And that, in turn, is only possible if their surfaces are precise to a thousandths of a millimeter. Find out how this is done – right here!
Machine frames and their components must exhibit ultra-precise surfaces in order to accurately fix machine elements such as guides, tables, slides, drives, measuring and testing equipment, spindles, and clamping devices. Depending on the casting mold geometry and design, dimensional, shape and positional accuracies of a few tenths of a millimeter can already be achieved on cast blanks.
After casting, the final accuracy requirements for these mounting surfaces as well as surfaces for sliding and hydrostatic guides are in the μm range, i.e. thousandths of a millimeter. These can be produced through various methods. Which of these is best suited depends on technical and economic aspects such as
- Number of planned parts
- Functions of the surfaces
- Size and weight of the frame components
- Complexity and position of the precision surfaces
Achieving highest accuracies on mineral casting blanks – this is how it is done!
The manufacture of high-precision functional surfaces on mineral casting components places high demands on the production process. Above all, the accuracy is influenced by the selected replication method and how it is carried out by man and/or machine; the material used is secondary. For example, hand lapping on mineral casting can be as precise as scraping on gray cast iron or steel.
The prerequisites for achieving maximum levels of accuracy are an air-conditioned production environment and a set-up strategy that is consistent – from replication, measurement, assembly, to machine operation.
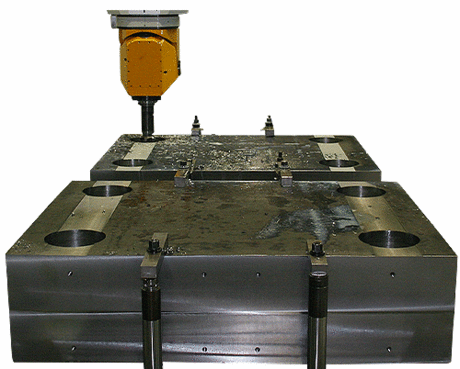
Milling
The mechanical processing of mineral casting parts with molded steel plates, cast plates, or steel strips is similar to the milling and drilling of machine components made of steel or grey cast iron on large and precise machining centers. Subsequent grinding and/or scraping of the steel parts with special hand-held scraping tools is possible. Milling special coating systems requires the careful selection of suitable tools.
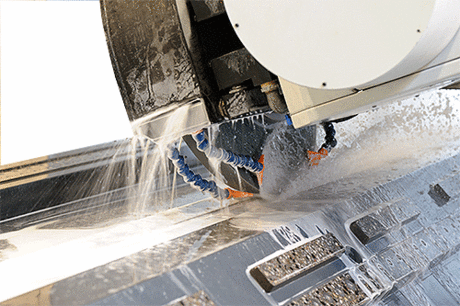
Grinding
The high-precision grinding of machine components made of mineral casting is carried out on high-precision surface grinding machines. The challenge lies in the exact coordination of speed, feed rate, and abrasive to the mineral casting and the cast-in thread steel inserts. The use of precise steel casting molds and the high accuracy of the mineral casting blanks produced here guarantee for economic grinding without pre-machining.
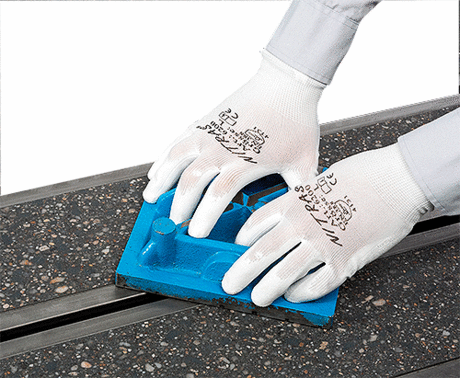
Hand lapping
The grinded surfaces can then be hand lapped. Using a lapping disc, a mixture of water or oil and finest grains is rubbed evenly on the mineral casting component. The loose grains roll over the surface and push the material aside with their grain tips, which is then broken out by the following grains. This way, high-precision guide or assembly surfaces are produced.
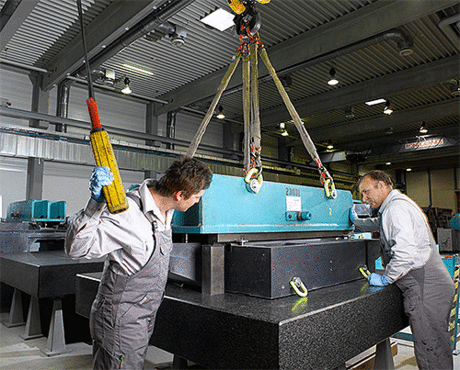
Non-cutting replication
If the production of molded precision surfaces takes place in temperature-controlled halls, is spatially separated from other production processes, and uses high-precision gauges, then an accuracy of fit of a few micrometers can be achieved on machine components. Very high demands are placed on the coating systems, also known as molding compounds (special resins with suitable fillers):
- High compressive strength
- Very hydrophobic
- High wear resistance
- Excellent sliding properties with good emergency running characteristics
- Smooth operating behavior (without stick-slip effect)
- Lapping
The molding compounds are mixed in dissolvers and then cast onto the mold or pumped into the space between the mineral casting blank and the impression gauge. Depending on the formulation, the gauge can be removed after 14 to 16 hours.
The key benefits:
- Excellent cost-efficiency, especially for medium to large quantities, as there is no costly use of machining equipment.
- The entire process is completed by RAMPF in-house – replicating in a climate-controlled work-shop at 20°C; no external processors or transport required.
- High reliability due to lack of influence from machines or tools.
- There is only a very small number of milling and grinding contractors that can reliably provide such high-precision results; using replication technology eliminates any dependency on these service providers (e.g. fluctuating capacities).
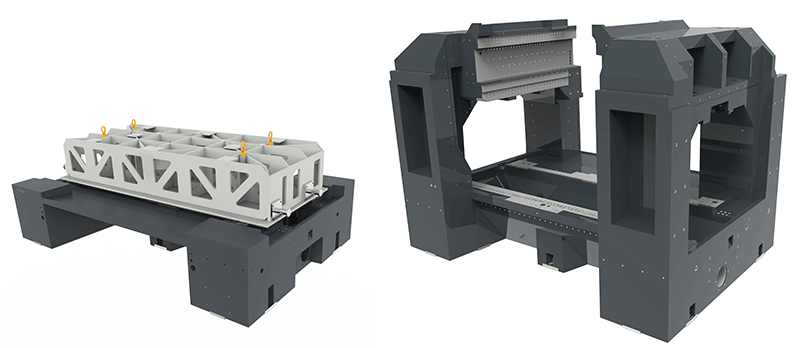
STAMA MT 733 milling-turning centers from the CHIRON Group are used around the world in numerous industries as a complete machining solution for productive and flexible series production and the manufacture of individual parts. The ultra-stable and ultra-precise machine beds are made of EPUMENT® mineral casting and manufactured in a special process using the innovative and cost-effective replication technology from RAMPF Machine Systems.