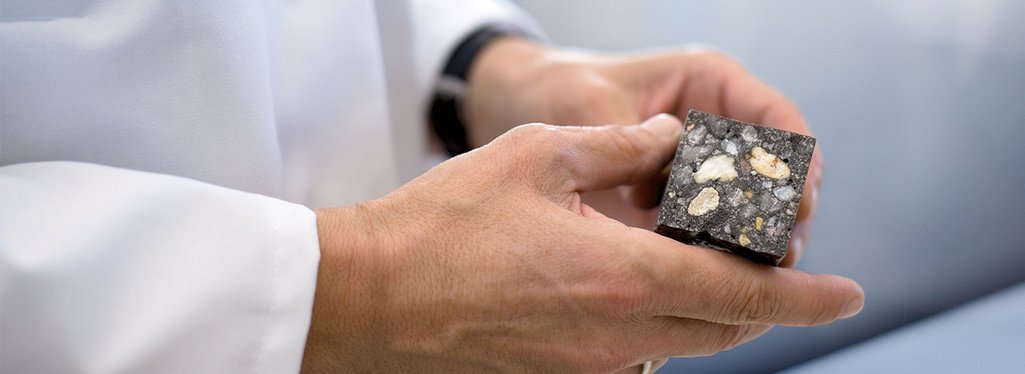
Mineral Casting – More Than Just The Right Ingredients!
EPUMENT® mineral casting for machine beds essentially consists of binders and fillers. Various additives are added to these two components. Only when the ingredients are of the highest quality, the recipe is perfectly coordinated, and the manufacturing process is carefully thought out and takes place in a controlled environment, can a top product be manufactured.
Binding agents
Important selection criteria for binding agents are modulus of elasticity, tensile and flexural strength, damping behavior, stress-free construction, molding accuracy, viscosity, processing time (pot life), hardening and curing time, as well as economic aspects. In addition, ecological considerations are also becoming increasingly important.
Essential requirements for mineral casting are a high modulus of elasticity and good damping behavior. The material should have low internal stresses, minimal cubic shrinkage for high molding accuracies, and a low coefficient of thermal expansion. For manufacturing, a long processing time is essential, especially for large-volume parts.
These requirements are best met with epoxy resins. In a polyaddition reaction, they react with the hardener without splitting off a low-molecular compound to form a three-dimensional network. Curing usually takes place with an aminic hardener, which reacts exothermically with the reactive groups of the epoxy resin at room temperature in an exact stoichiometric mixing ratio.
Modification and additives
Via a combination of the reactants with modification aids, e.g. a reactive diluent to lower viscosity, and various additives to improve reaction, adhesion, and ventilation, a technically optimized binder system can be developed for every requirement profile.
Fillers
Mineral casting for mechanical engineering is mainly produced from inorganic mineral fillers such as quartz sand, quartz gravel, and crushed rocks such as granite and basalt. For specific applications, synthetic materials such as aluminum hydroxide, silicon carbide, iron powder, or glass spheres are occasionally used.
Important selection criteria for the fillers are high modulus of elasticity, excellent compressive strength, resistance to moisture and chemicals, good wettability, high packing density to minimize the consumption of binding agents, as well as physiological and economic considerations.
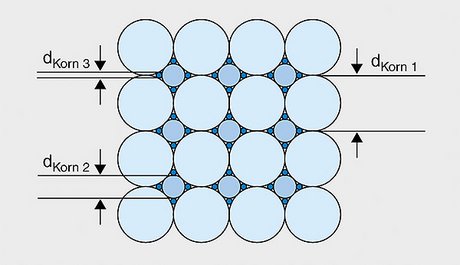
Grain matrix
Mineral casting systems for mechanical engineering contain fillers in various grain size ranges, starting with less than 0.1 mm (stone powder) over 0.1 mm to 2 mm (sand), and up to 16 mm (gravel). The best alignment of up to ten different grain fractions to form a sieve line with a high packing density makes it possible to reduce the space to be filled by the binder to a minimum and to derive forces acting on the mineral casting as best as possible via the load-bearing grain matrix.
Dr. Thomas Abel, Director of Laboratory at RAMPF Machine Systems
EPUMENT® mineral casting is used worldwide by renowned customers in classic machine tool construction as well as applications in the semiconductor, laser, medical, and packaging industries. In the European, US, and Asian markets, we develop and produce in our own factories, which enables us to guarantee uniform quality and just-in-time delivery.