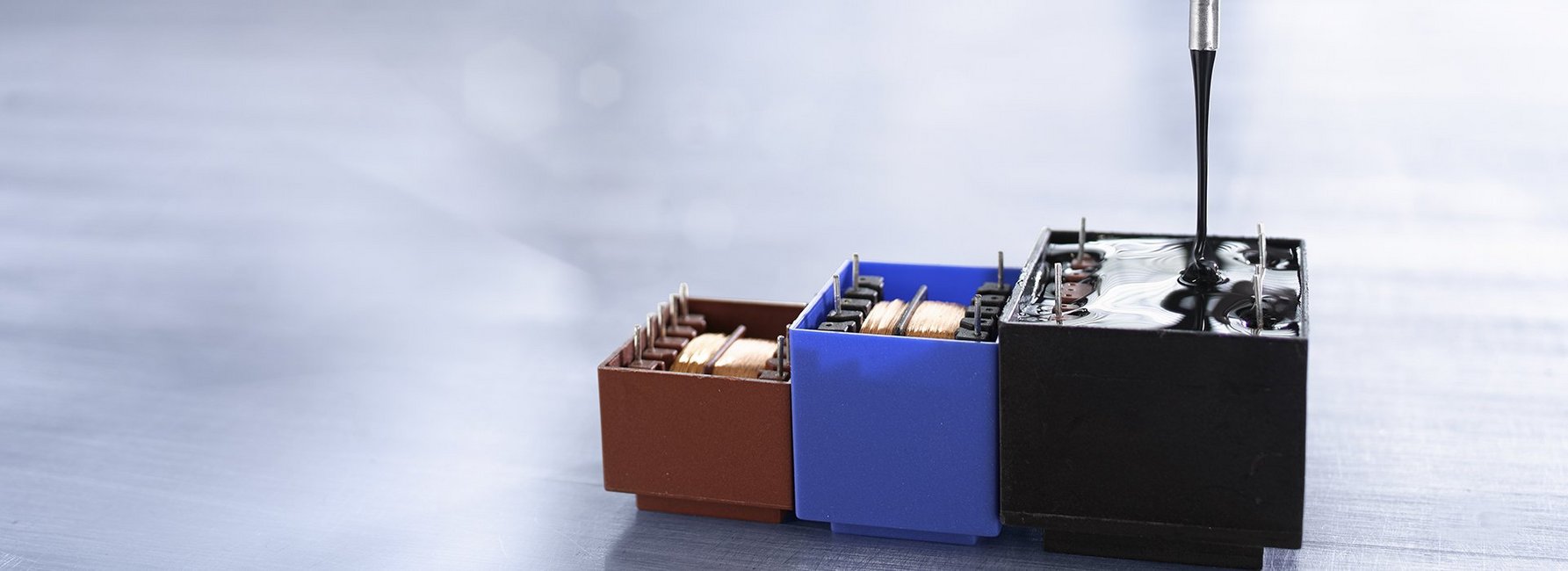
For Electrical and Electronic Components
Electro Casting Resins (potting/encapsulating)
Electro casting resins are key to the further development of numerous industries. The automotive, energy, automation, and household goods industries are all heavily dependent on developments in storing and transferring electricity.
One- and two-component electro casting resins from RAMPF Advanced Polymers boost components’ reliability and performance while also ensuring cost-efficiency and a long service life. They give your components (transformers, control units, inverters, motors, etc.) reliable and efficient protection against chemical substances and environmental influences such as heat, cold, and moisture.
Customers using our products based on polyurethane (RAKU® PUR), epoxy (RAKU® POX), and silicone (RAKU® SIL) include leading manufacturers in the automotive and electronics industries.
These products also boast a wide range of mechanical, thermal, and chemical properties. They ensure low thermal stresses by efficiently conducting heat away from your component.
Even in the event of extreme temperature changes, the material retains sufficient elasticity to reduce stresses occurring in the component.
Our first-rate materials are complemented by the extensive application expertise of RAMPF Production Systems, one of the world’s leading specialists for mixing and dispensing technology and automation solutions.
Material, machine, process – benefit from RAMPF’s highly competent complete service.
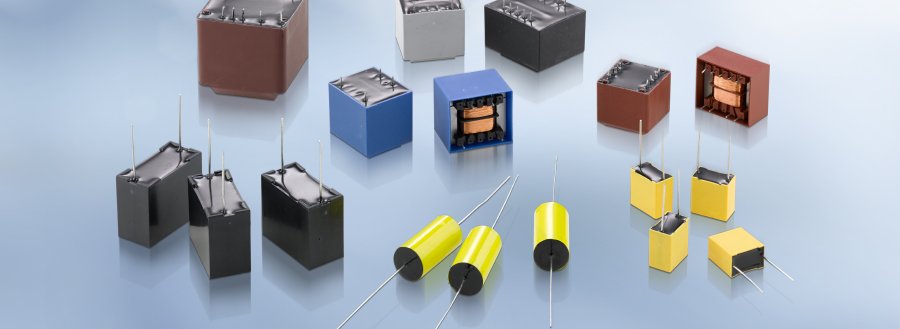
Your key benefits
- High mechanical and thermal strength ensures the long-term functionality of your application
- Broad scope of applications thanks to innovative, customized product development
- High thermal conductivity
- High resistance to fluctuations in temperature
- More than 35 years of experience in developing and manufacturing innovative electro casting resins
- Wide range of properties optimized in line with your requirements
- Our products comply with RoHS and test standards/listings such as UL 94, RTI, OBJS2, etc.
- Used by leading manufacturers in the automotive and electronics industries
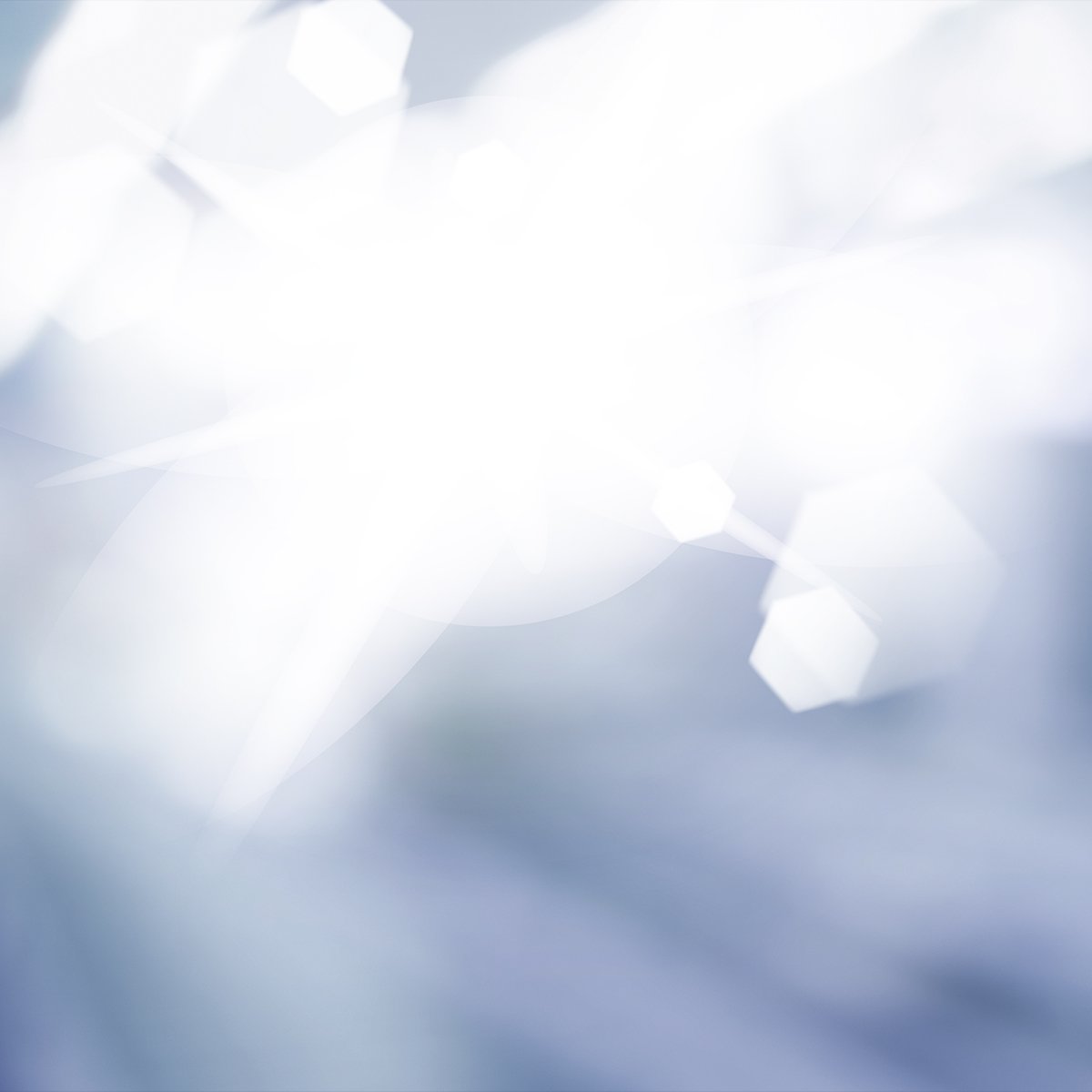
Application images
Material types
Chemical reaction
- Two-component
- Polyaddition reaction
- Minimal exothermic reaction
- Cures at room temperature
- Curing conditions can be flexibly adjusted by adding a catalyst
- Low shrinkage pressure on cast components
Area of application
- Temperature range: -60 to +155 °C, short-term: +160 °C
- Wide range of mechanical properties, from tough to highly elastic
Properties
- Excellent resistance to fluctuations in temperature for sensitive components
- High crack resistance for flexible products
- Good chemical resistance
- Low water absorption
- Impressive electrical properties
- Tg: from -75 to +120 °C
- RTI: to 155 °C
- OBJS2-listed
Adhesion
- Good adhesion to housings and components
- Good adhesion to plastics such as PA, PBT, and ABS
Flame retardancy
- Can be adapted to UL 94 V0
Chemical reaction
- One or two components (1C or 2C)
- Homopolymerization (1C) and polyaddition reaction (2C)
- Cures at room temperature
- Curing can be accelerated using heat
- Heat curing required for one-component and hot-curing epoxy
- Good impregnation properties
- Low sensitivity to moisture
Area of application
- Temperature range: -40 to +180 °C, short-term: +200 °C
Properties
- High thermal dimensional stability
- Low coefficient of thermal expansion
- High dielectric strength
- High media resistance to fuels
- Low water absorption and water vapor permeability
- Tg: -20 to +180 °C
- OBJS2-listed
Adhesion
- Good adhesion to metals
Flame retardancy
- Can be adapted to UL 94 V0
Find here more information on processing diisocyanates according to REACH, Annex XVII, Entry 74:
Chemical reaction
- One or two components
- Polyaddition and polycondensation reaction
- Minimal exothermic reaction
- Cures at room temperature
- Curing can be accelerated using heat
- Curing without by-products possible (polyaddition reaction)
- Low shrinkage pressure on cast components
- Low sensitivity to moisture
- Hydrophobic
Area of application
- Wide temperature range: -60 to +200 °C, short-term: +250 °C
- Optimum physical properties, virtually constant over the entire application temperature range
Properties
- Very good resistance to temperature fluctuations
- High crack resistance
- Excellent chemical resistance for extreme environments
- Low water absorption
- High water vapor permeability
- Impressive UV and weather resistance
- Tg: always < 0 °C
Adhesion
- Good adhesion to mineral substrates
- Adhesion to other substrates often only with pre-treatment
Flame retardancy
- Can be adapted to UL 94 V0
Contact us to discover the perfect material for your application.
We’ll give you all the help you need with your processes – from original idea to finished product.
With production sites on three continents and sales partners worldwide, we’re always there for you.
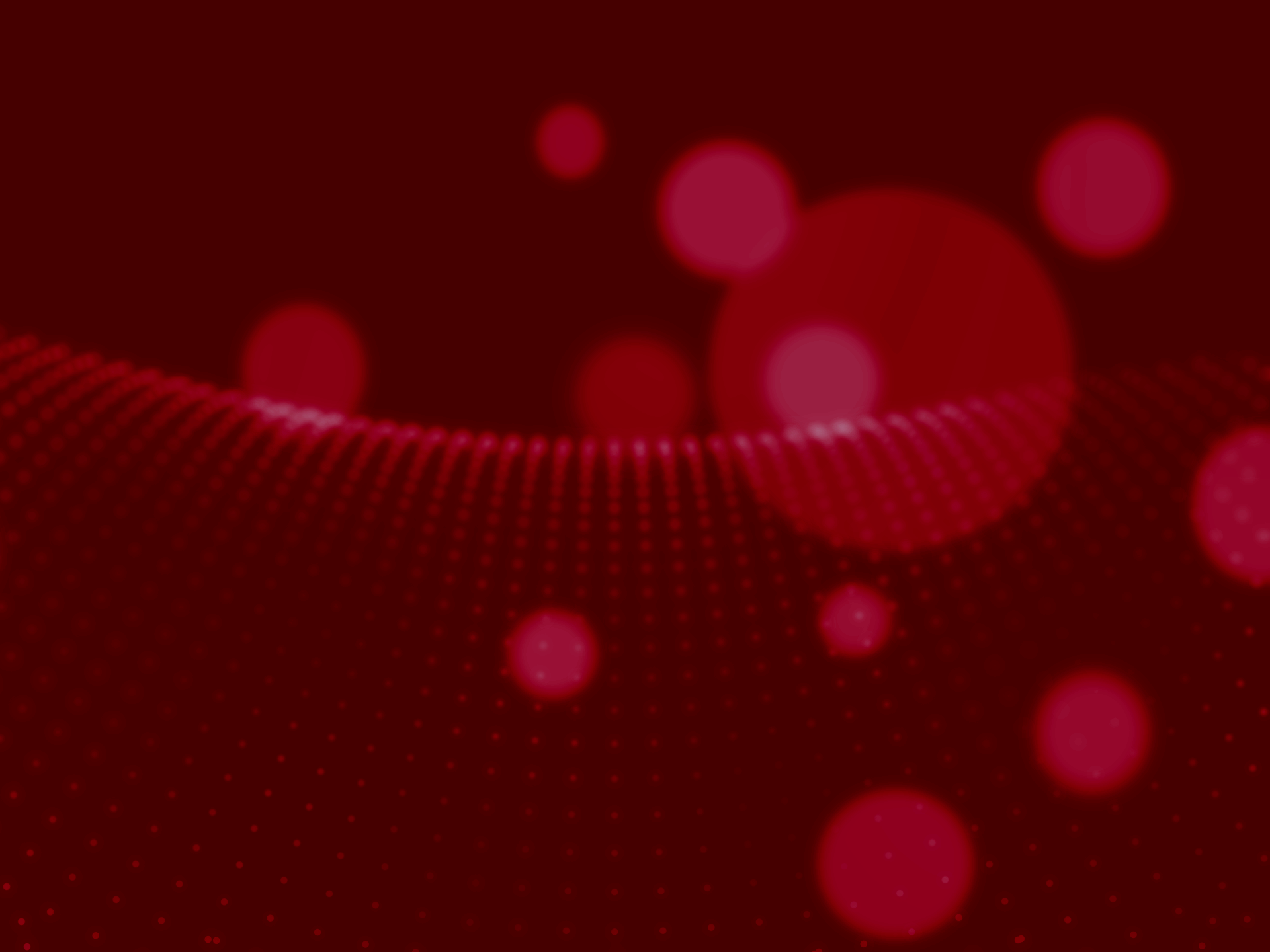
RAMPF Contact
Contact us – worldwide and around the clock!
- Please select