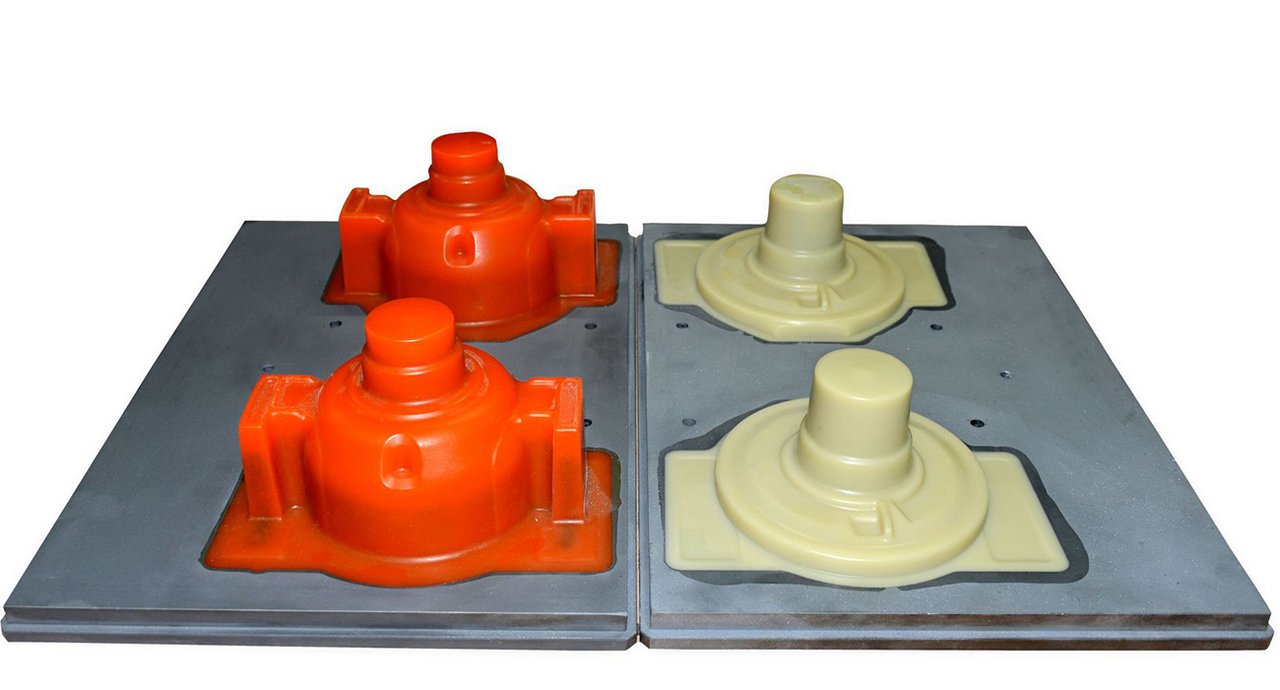
RAMPF erhält Patent für Frontguss-System und Herstellungsprozess
RAMPF Tooling Solutions, ein führender Entwickler und Produzent von Block- und Flüssigmaterialien sowie Halbzeugen für den Modell- und Formenbau, hat für sein Frontguss-System RAKU-TOOL® PC-3458 / PC-3459 / PH-3958 vom Deutschen Patent- und Markenamt in München das Patent erhalten – Patentnummer 10 2012 102 852. Das Schutzrecht bezieht sich sowohl auf das Gießharz als auch auf den Herstellungsprozess im Frontgussverfahren.
Mit dem Frontguss-System RAKU-TOOL® PC-3458 / PH-3958 setzt RAMPF Tooling Solutions neue Maßstäbe im Bereich Flüssigprodukte für die Gießerei. Mit dem hoch abriebbeständigen Material wurden in der Praxis bereits mehr als 200.000 Abformungen erzielt. RAKU-TOOL® PC-3458 / PH-3958, das direkt am Folgetag einsetzbar ist und bis zu 25 Kilogramm handvergossen werden kann, ist das einzige System auf dem Markt mit einer Wärmeformbeständigkeit (HDT-B) von 95 °C. Somit können in der Praxis höhere Prozesstemperaturen gefahren werden, was nachhaltig die Produktionskapazität erhöht.
Das Frontguss-System ist aufgrund der erzielbaren Abformstückzahlen besonders geeignet für die Großserienproduktion von Kernkästen und Formplatten. Das Material punktet durch
- die sehr hohe Dimensionsstabilität,
- die Maßhaltigkeit der Gießereieinrichtung (Metall-Hinterbau),
- die sehr hohe Chemikalienbeständigkeit,
- das Ausbleiben von Aufquellen,
- die sehr geringe (bis keine) Sandanhaftung sowie
- Kostensenkungen in der Instandsetzung, da nur die Frontgussschicht erneuert werden muss, wenn die Verschleißgrenze erreicht ist.
Auf mehr als 80.000 Abformungen in der Praxis kommt das Frontguss-System RAKU-TOOL® PC-3459 / PH-3958. Das beigefarbene System ist nach fünf bis sieben Tagen Härtung bei Raumtemperatur einsetzbar. RAKU-TOOL® PC-3459 / PH-3958 hat eine HDT-B von 65 °C und kann bis circa 110 Kilo-gramm handvergossen werden.
Frontgussverfahren: Hohe Abformungszahl, geringer Aufwand
Der Hauptvorteil des speziell auf das RAKU-TOOL® PC-3458 / PC-3459 / PH-3958 Gießharz abgestimmten und patentierten Verfahrens ist, dass die unterdimensionierten Grundkörper nach dem Verschleiß der Oberflächen mit geringem Aufwand wieder neu beschichtet werden können. Beim Frontgussverfahren werden folgende Herstellungswege für Formplatten und Kernkästen angewandt:
1. Bei der Herstellung von Formplatten wird zuerst ein Urmodell oder eine Prototypenformplatte erstellt. Von dieser wird ein Negativ abgenommen. Anschließend wird ein unterdimensionierter Hinterbau, der aus den unterschiedlichsten Materialien wie Holz, Kunststoff oder Metall bestehen kann, für den Frontguss erstellt. „Das wesentliche Kriterium der Materialauswahl für den Hinterbau ist die zu erzielende Qualität hinsichtlich Stabilität und Maßhaltigkeit“, so Marcus Vohrer, Leiter Anwendungstechnik bei RAMPF Tooling Solutions. Der gefertigte Hinterbau und das Negativ werden miteinander maßhaltig montiert.
2. Um einen Kernkasten im Frontguss herzustellen, wird zuerst eine Kernseele angefertigt, die den eigentlich gewünschten Sandkern als Modell darstellt. Der Trägerkörper des Kernkastens wird je nach Qualitätsanspruch aus Holz, Kunststoff oder Metall mit Aufmaß zur Kernseele gefertigt. Die Kernseele wird mittels Teilungsebene (Formstand) mit dem Trägerkörper montiert. Das jeweilige Gießen der Frontgussschicht erfolgt über den Eingusspunkt, welcher an der tiefsten Stelle der Kavität liegen sollte. Die Frontgussschicht ist die Nutzfläche und somit die am meisten beanspruchte Fläche. Der Frontguss kann von Hand oder mit Misch- und Dosieranlagen erfolgen.
„Mit unserem patentierten Frontguss-System und dem dazugehörigen Herstellungsprozess verschaffen wir unseren Kunden in der Gießerei-Industrie entscheidende Wettbewerbsvorteile“, so Jochen Reiff, Vertriebs- und Marketingleiter bei RAMPF Tooling Solutions. „Durch die hervorragende Abrasionsbeständigkeit und Wärmeformbeständigkeit ist das System in Leistung und Qualität auf dem Markt unübertroffen, was unseren Kunden schlussendlich Kosten und Zeit spart.“