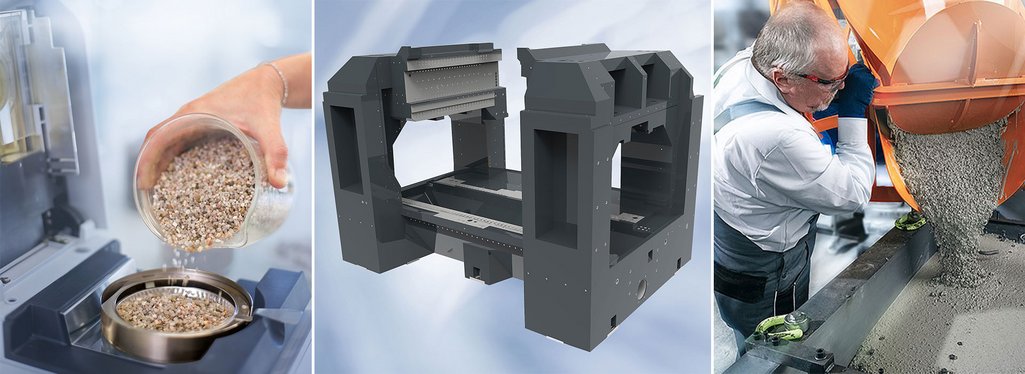
So wird's gemacht – Teil 1: Die Herstellung von Mineralgussteilen
Von der Erstellung der Gießform über das Mischen der Mineralguss-Ingredienzen bis zum Lackieren des fertigen Teils: Wir erzählen die spannende Entstehungsgeschichte eines Hightech-Maschinengestells aus EPUMENT® Mineralguss von RAMPF Machine Systems.
- Gegenüber metallischen Werkstoffen besitzt er eine signifikant bessere Dämpfung, was eine höhere dynamische Stabilität der Gestellstruktur in ultraschnellen und hochpräzisen Produktionsmaschinen gewährleistet.
- Seine thermische Stabilität ist herausragend, das Verhalten gegenüber kurzzeitigen Temperatureinflüssen somit sehr träge.
- Dank der ressourcenschonenden Herstellung sowie umweltverträglichen Entsorgung und Verwertung hat er eine herausragende ökologische Bilanz.
Und das sind nur drei von zahlreichen weiteren Vorteilen von EPUMENT® Mineralguss.
Es überrascht daher nicht, dass der innovative Werkstoff sich längst im Hightech-Maschinenbau etabliert hat und rund um den Globus in immer mehr Branchen eingesetzt wird – sowohl in Anwendungen im klassischen Werkzeugmaschinenbau als auch in der Halbleiter-, Laser-, Medizin- und Verpackungsindustrie.
Doch wie entstehen aus Mineralien, Gesteinen und Epoxidharzbindemittel derart leistungsfähige Gestellstrukturen?
So wird's gemacht:
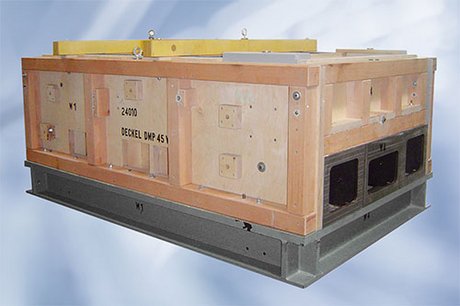
1. Herstellung der Gießform
In der Regel werden Gießformen von spezialisierten Werkzeug- und Formenbauern gefertigt und bei diesen abgenommen. Der Vorteil: eventueller Fehler und Abweichungen können umgehend korrigiert werden. Nach der Abnahme wird die Gießform an RAMPF Machine Systems geliefert, in ihre Einzelteile zerlegt und auf Montageböcke oder -vorrichtungen gelegt oder stehend fixiert.
2. Reinigen und Beschichten mit Trennmittel
Die Innenseiten der Gießformsegmente müssen gereinigt werden. Um zu verhindern, dass der Mineralguss mit den Innenseiten der Gießformsegmente verklebt, wird die komplette Innenfläche der Form mit einem speziellen Trennmittel beschichtet, in der Regel durch Sprühen. Eingießteile wie Gewindeanker, Fußplatten und Rohre werden durch Verschrauben beziehungsweise Aufstecken an der an der Innenseite der Gießform fixiert.
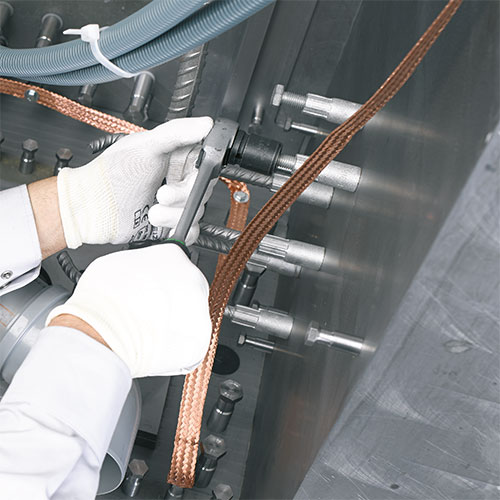
3. Auftrag des Gelcoat
Danach wird ein Gelcoat durch Streichen oder Airless-Spritzauftrag in einer Schichtstärke von 0,5 mm bis 2 mm auf die Innenseiten der Formteile aufgebracht, jedoch nicht auf abzuformende oder zu verklebende Flächen. Das Harz hat die Aufgabe, sich mit dem eingegossenen Mineralguss zu verbinden und eine widerstandsfähige Oberflächenschicht zu bilden. Eigenschaften wie Kratzfestigkeit und Temperaturbeständigkeit können an Kundenanforderungen angepasst werden. Das Gelcoat kann in den meisten RAL-Farben hergestellt werden und dient als Grundierung für eine anschließende Lackierung. Abschließend werden die Formteile miteinander und mit dem Formboden verschraubt und verstiftet.
4. Dosieren, Mischen, Gießen, Verdichten
Die Bestandteile des Mineralgusses werden dosiert, gemischt und in die Gießform vergossen. Nach einer Verdichtung erfolgt die Aushärtung in der Gießform.
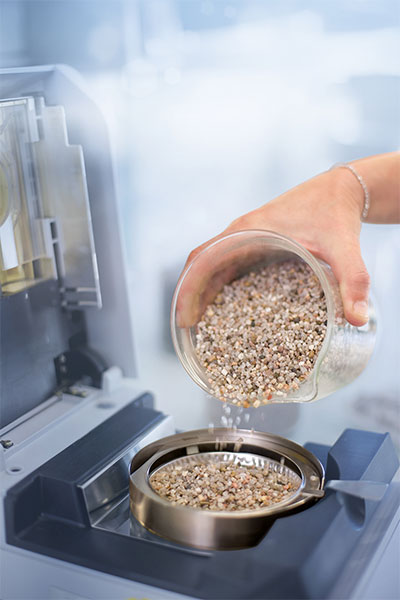
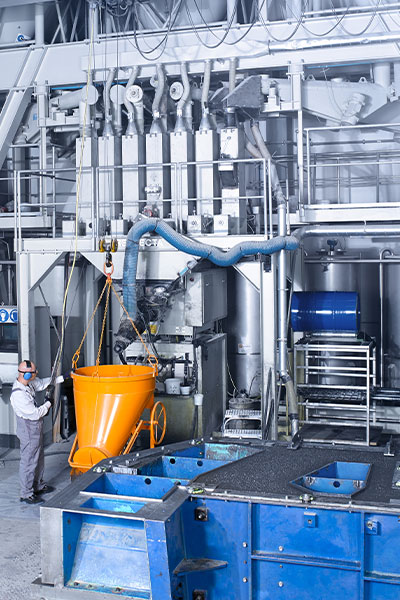
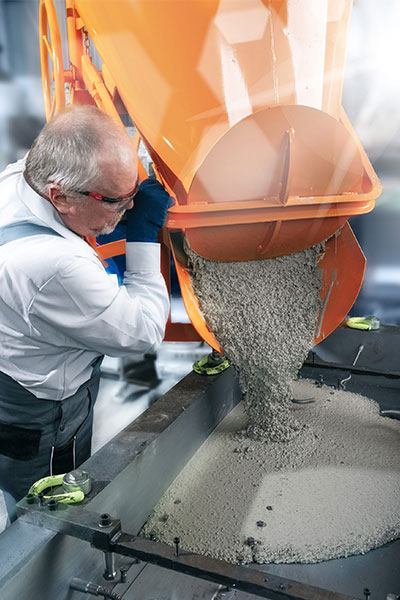
5. Verdichten
Der Verdichtungsprozess dient der bestmöglichen Entlüftung der Mineralgussmischung und Verbesserung des Fließverhaltens der relativ zähen Masse. Durch die Relativbewegung der Füllstoffbestandteile beim Rütteln wird der Porengehalt verringert. Insbesondere beim Verdichten großvolumiger Teile in schweren Gießformen werden mit sogenannten Verdichtungstischen bessere Ergebnisse erzielt. Der Einfluss von Parametern wie Beschleunigung, Amplitude, Frequenz und Zeit auf das Verdichtungsergebnis und damit auf die Endeigenschaften des Mineralgusses sind theoretisch untersucht. In der industriellen Praxis werden diese Parameter für jedes Gussteil abhängig von Füllgewicht, Füllhöhe und Gießformwerkstoff individuell festgelegt. Moderne Verdichtungstische sind bis zu einer Frequenz von 70 Hz und bis zu einer Beschleunigung von 25 m/s2 (2,5 g) stufenlos regelbar.
6. Aushärten
Für das Aushärten wird die gefüllte Gießform in der Montagehalle exakt eben aufgestellt, da durch die verschränkte Lage der Gießform während des Aushärtens ein nicht maßhaltiger Gussrohling entstehen würde. Weil Stahlformen Wärme schneller von außenliegenden Mineralgussschichten ableiten als aus dem Kern, ist bei großen Gestellbauteilen eine Wärmeisolierung der Gießform zu empfehlen. Ziel ist es, die Temperaturentwicklung über den gesamten Querschnitt des Gussteils gleichmäßig zu gestalten, was durch eingegossene Temperaturfühler kontrolliert werden kann. Die Geschwindigkeit der Aushärtung wird durch die Außentemperatur und die Reaktivität des Härters beeinflusst. Nach 12 bis 14 Stunden Aushärtung in der Gießform kann der Gussrohling entformt werden. Somit ist in der Regel je Arbeitstag ein Mineralgussteil pro Gießform herstellbar.
7. Entformen
Bei der Demontage der Gießform werden die Befestigungsschrauben der Eingieß- und Losteile der Gießform entfernt und die Formteile in umgekehrter Reihenfolge der Montage vom Gussrohling abgedrückt. Anschließend wird der Gussrohling vom Formboden gehoben und sämtliche losen Teile werden aus dem Rohling entfernt.
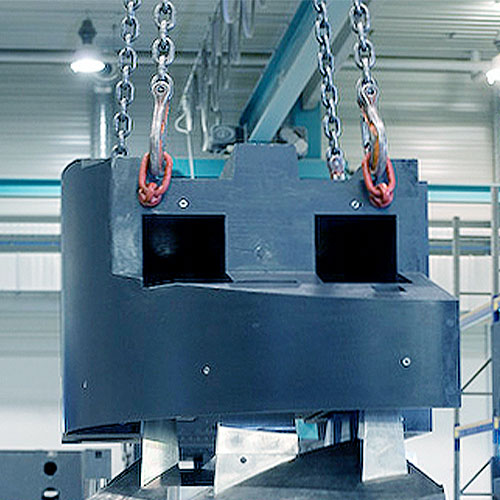
8. Putzen
Bedingt durch den Kaltguss in präzise Formen und dank leistungsfähiger Gelcoatsysteme ist das Putzen von Rohlingen aus Mineralguss generell weniger aufwendig als bei jenen aus Grauguss. Die Oberflächen haben bereits eine gute optische Qualität und genügen oftmals schon nach dem Abwaschen des Trennmittels den gestellten Anforderungen. Gestellbauteile, die Design- und Verkleidungsfunktionen an Maschinen übernehmen, müssen an den entsprechenden Flächen geputzt werden. An den Fügeflächen der Gießformsegmente entstehen am Gussrohling Grate, welche mit Handschleifern abgeschmirgelt werden; auch andere Oberflächenmängel wie Ausbrüche, Abdrücke oder Oberflächenlunker werden beim Putzen beseitigt. Vor dem Lackieren wird die Gelcoatoberfläche angeschliffen. Eine weitere Aufgabe des Putzens ist die Vorbereitung von Flächen, die in einem nächsten Prozessschritt abgeformt oder verklebt werden. Diese Flächen sind, wie bereits erwähnt, nicht mit Gelcoat beschichtet. Die Mineralgussoberfläche wird mit Handschleifern aufgeraut. Nach dem Abformen oder Verkleben werden Überstände abgeschliffen.
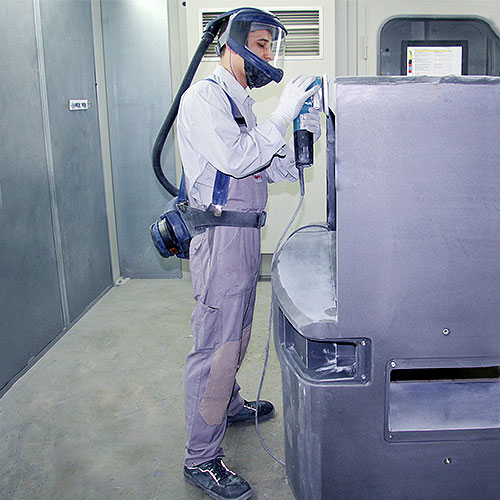
9. Veredelung der Eingussfläche
Die Eingussfläche ist offen, nicht formbestimmt, und aus diesem Grund leicht uneben. Das stört in der Regel allerdings nicht, da es sich meist um die Gestellunterseite handelt. Bei höheren Anforderungen kann diese Fläche durch Aufbringen (Aufgießen) eines Gießbelags optisch veredelt werden.
10. Lackieren
Mineralgussteile können in praktisch jeder Farbe lackiert werden, das Aufbringen des Lacks erfolgt durch Spritzen oder Walzen. Da bereits viele Eingießteile im Rohling integriert sind, ist auf den Schutz von Innengewinden zu achten. Trenn- und Reinigungsmittel, Gelcoat und das Lacksystem chemisch müssen aufeinander abgestimmt werden.
Das Resultat kann sich sehen lassen, wie unter anderem das Maschinenbett (links) des MT 733 one plus »Chuck« Fräs-Dreh-Zentrums von STAMA (rechts) eindrucksvoll unter Beweis stellt:
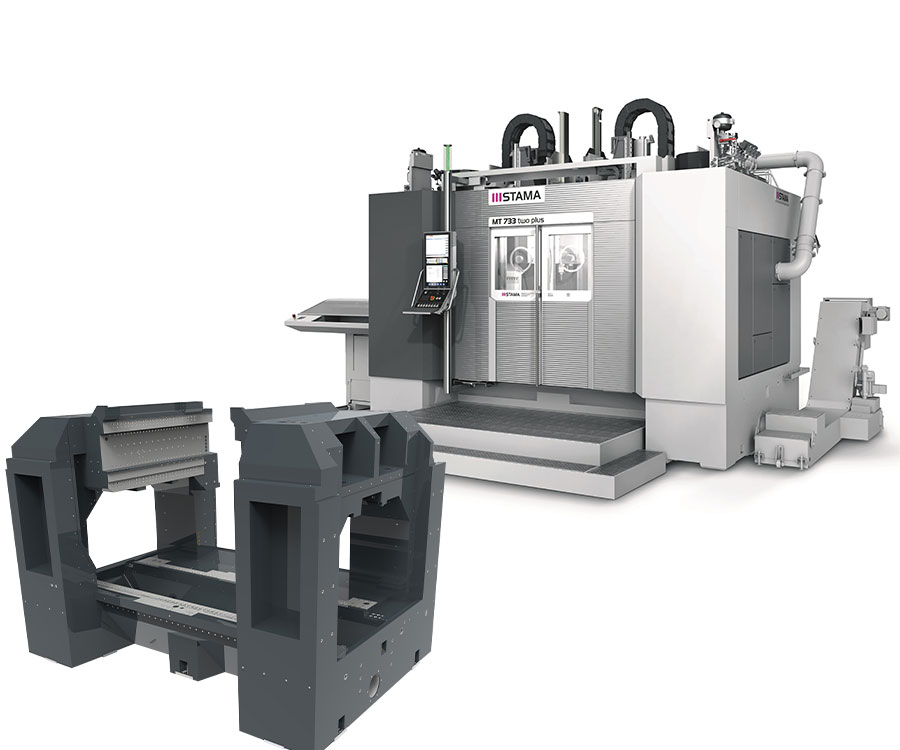